Günther+Schramm (G+S), a system service provider for steel and aluminium, with its main warehouse located in Königsbronn, Germany, decided to upgrade its high-bay storage system with the help of Kasto. Just four weeks after the modification of the bar storage system, the operations were running smoothly and efficiently.
Located in Achern, Germany, the Kasto Group specializes in sawing, storage and automation technology for metal bar stock. The company designs and builds metal sawing machines, semi-automatic and automatic storage systems for metal bar stock and sheet metal, automated handling equipment for metal bars, sheets and cut-pieces including the necessary software. With 180 years of experience, Kasto holds 170 patents, has built more than 140,000 sawing machines and has installed more than 2,400 automated storage systems. Besides the subsidiary plant in Schalkau, Germany, Kasto also operates subsidiaries in England, France, Singapore, China, Switzerland and the United States.
Günther+Schramm employs around 180 individuals and supplies more than 60,000 tonnes of metals and plastics annually to southern Germany and neighboring countries. In addition to the quality and reliability of its products, the metal distributor prioritizes delivery dependability. The company understands the importance of timely delivery and ensures that all goods can be retrieved promptly at any time by maintaining a smoothly functioning materials warehouse.
"This is exactly where we repeatedly reached our limits," recalls Michael Sticke, assistant operations manager at G+S’ Königsbronn warehouse, making him responsible for the high-bay storage system. After approximately 30 years of operation, the mechanics were causing issues regularly, and downtimes became more frequent.
"This was a classic example of the bathtub curve," says Sticke. This type of diagram can be used to illustrate the typical service life of a device graphically. In the initial phase, the failure rate decreases, followed by a long period without any issues. Finally, aging and wear lead to more frequent failures, and the curve rises steeply.
"After such a long period of operation, it was exceedingly difficult to acquire spare parts,” explains Sticke. “We were always at risk of waiting a week or two for a new component and making us unable to serve our customers in the meantime."
The decision was made: it was time to update the existing Kasto SNLS 5000/7100 S bar storage system, which was the predecessor of the Kasto Unitop. This high-bay storage system has a payload of 5,000 kg per cassette and a storage length of 7,100 mm. "We are very pleased with the technology provided by Kasto, and, in addition to the storage system, we also utilize various sawing solutions such as the Kastovariospeed C 15, equipped with the Kastosort robot handling system. Therefore, it was obvious to us that we would tackle the extended retrofit together with Kasto," emphasizes Sticke. Something else was essential: the project had to be completed swiftly because, without a functioning bar storage system, G+S would be unable to supply its customers.
Complete overhaul
G+S and Kasto went all-out during the modernization process, retaining only the steel structure and cassettes while replacing everything else (Figure 1). "We replaced the operating gantry crane, the undercarriage and two four-way circulating stations," explains Alfred Schwörer, sales and project manager retrofit at Kasto. "As part of this endeavor, we also updated the safety and control technology, an absolute must (Figure 2)."
The entire modernization was to be completed in four weeks. "That was a very ambitious task," affirms Schwörer, "yet we succeeded." Kasto embarked on the project with a detailed schedule and was strongly supported by the G+S employees. Work began with opening the roof of the high-bay storage system to lift the old operating gantry crane out of the building by crane (Figure 3). Carpenters installed a platform directly under the hall roof in advance to ensure that the work at lofty heights for the employees was safe. With up to seven of its own employees, Kasto then installed the systems and replaced the control and safety technology.
Complete update of the old storage system
The core of the retrofit is the new operating gantry crane with traveling gear, lifting gear and load beam. The roller bearings are lubricated for life. The frequency-controlled three-phase ac drive enables the device to be positioned precisely through power transmission with pre-stretched precision roller chains selected in sets. The system is supplied with energy through a wear-free and fail-safe energy chain. The cassettes can be accessed quickly, thanks to the system design. "The design is focused on process reliability, which is exactly what we need to ensure delivery capability at all times," explains Sticke.
The interconnection of the intermediate drive circuits of all movement axes, including the hoist drive, enables energy exchange within the system. For instance, the surplus energy produced during braking processes can be used to operate other axes. The entire drive system, including the hoist, feeds surplus energy back into the customer's grid. "This approach enables us to create an efficient and sustainable solution that makes optimum use of resources," says Schwörer.
Quick order picking system thanks to the undercarriage
The updated undercarriage now features two spaces on roller frames. Thanks to Kasto's traveling cassette principle, storage and retrieval operations can take place simultaneously, optimizing the number of movements required. Like the operating gantry crane, the roller bearings are lubricated for life. A servo inverter controls the drives continuously, while an electronic synchronization function minimizes positional deviations between the two drives.
The updated storage system also includes two customized circulating stations in connection with the undercarriage for storing and retrieving cassettes. These stations consist of a 2-by-9 m roller frame located outside the shelving system. All rollers are mounted on ball bearings and powered by a frequency-controlled three-phase motor, guaranteeing maximum energy efficiency and optimal operational processes.
Central intelligence for increased safety and comfort
Given that G+S already used a Kasto control system, the old Kastolvr software required updating to Kastologic. This update provided the metal distributor with improved performance, new functions and features tailored to its processes (Figure 4). For instance, order history is now available, user rights can be managed via groups, and operator input through the dialogue interface is closely monitored. Apart from the basic functions, G+S uses the Stock Production module to manage stocks and production.
"The graphic interface with a standardized operating philosophy offers a successful user experience and supports the specialized staff in their work in the warehouse," Schwörer states.
Employees access the circulating station from a control panel for the Kastologic Client. In addition to the display, label printer and manual operational controls, the new solution also features weighing electronics. The menu navigation supports the operators during storage and retrieval. "Kasto provided our employees with training and familiarized them with the new screen," explains Sticke. "After so many years, they needed to become accustomed to working with a new system, but they quickly adjusted to the new processes."
Ready for the future
The next step is to link the Kasto environment with the SAP world. This will allow order data to be created and maintained directly in Kastologic without the need to switch to the SAP ERP. "Although this only requires a minimal amount of time per order, it does accumulate since we have many orders," explains Sticke.
Once again, the collaboration with Kasto proved very successful, Sticke reports. "The detailed schedule ensured that we always knew exactly where we were and what would happen next,” he says. “After two weeks, Kasto installed all the systems, and the programmers were able to start fine-tuning."
Nonetheless, the retrofit was an exciting process. "It was definitely well worth it since we are now well-equipped for the future and can once again provide dependable deliveries", explained Sticke, who jokingly added, "However, I am glad that my successor will be in charge of the next retrofit in 30 or 40 years."
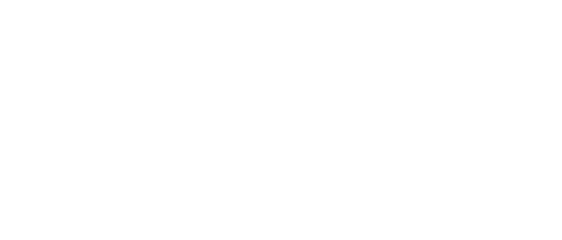
Leaders relevant to this article: