The language used by suppliers of technology solutions aimed at precision engineering applications is vague and in some instances confusing. Words such as “precision” and “resolution” without any degree of qualification are just meaningless. When looking at motion-control solutions that provide sub-micron and nanometer-level accuracy, a new language is necessary, and new standards are required to indicate the real levels of precision that different motion-control solutions can achieve.
There are times when technological advancements are such that they necessitate a root and branch change in the language and nature of discussion associated with them.
When electricity became available in every home, it would have been somewhat perverse if we had all continued to talk in terms of our preferred candles rather than the relative luminescence and longevity of various forms of light bulbs. Likewise, when the car began to emerge, and eventually replaced the horse and cart as the most efficient form of transportation, the discussion logically switched from the best hay to feed the horse to the merits of different forms of internal combustion.
Without stretching this analogy to the breaking point, there is a similar shift in the area of motion control. A new technology has emerged that pushes the boundaries of what is deemed possible in terms of precision to such an extent that the language surrounding the technology has to change, and the nature of the conversation needs to shift in order to differentiate this new technology from standard industry alternatives.
The technology in question is our Hybrid Hexapod (Figure 1). We are in blue-ocean territory here. In the past 20-25 years, there has been more and more interest in hexapods to cater for the increased demand for micron, and sub-micron level precision in multi-axis motion applications. Hexapod motion-control technology exists at the ultra-precision end of motion control, and it has been the best-in-class motion control solution for exacting industrial applications for a couple of decades.
Figure 1: The Hybrid Hexapod represents a step forward in motion control and provides the ability to achieve repeatable nano-level accuracy, stimulating innovation and promoting manufacturing efficiency.
The burgeoning area of more and more precise motion control is driven by industry demand for technologies that will improve production processes. The emphasis from across industry is for smarter, smaller and faster precision motion control and positioning equipment, and demand is especially high in areas such as laser micro machining, micro assembly automation, optical inspection, semiconductor metrology and photonics components test and alignment applications.
The Hybrid Hexapod represents a quantum step forward in motion control and for the first time provides the ability to achieve repeatable nano-level accuracy, stimulating innovation and promoting manufacturing efficiency.
One key area for focus is how motion control process suppliers describe the level of precision achievable. Standard industry vernacular talks in terms of micron and sub-micron precision, but we are now working with the National Institute of Standards and Technology (NIST) to move to a new and more effective methodology of measuring and quantifying motion systems by introducing the concept of Point Precision.
Figure 2: In the area of motion control, the focus should and must be on exacting criteria, by which we mean repeatability and accuracy.
What does precision mean?
The very nature of the word “precision” is vague. You might be used to hearing descriptions using phrases such as “precise” and “ultra-precise.” Also, you will be used to reading claims of achievable “resolution.” But what does resolution really mean, and what does it tell you?
In the area of motion control, the focus should and must be on much more exacting criteria, by which we mean repeatability and accuracy. Precision is actually synonymous with repeatability and accuracy, but too often suppliers hide deficiencies in these areas behind meaningless phrases such as precision, high accuracy, high precision, or ultra-precision. When looking at the Hybrid Hexapod, precision means 10 nanometers or less, repeatably.
For standard hexapods, claims of precision are best condition, unidirectional one-axis numbers, which don’t factor all six-axis error quotients or the backlash, which is the total error of all motion in a hexapod due to the compression and tension of each leg for every move. Claims made for conventional hexapods may be designed to look like a similar duck to claims made by real nanometer accurate motion-control solutions, but from the perspective of Point Precision they do not quack in nanometers but tens of microns.
Unless the word precision is accompanied by such quantifiable and definite statements in terms of what is achievable, it is truly meaningless. While still vague, micron, sub-micron, and nano precision are better. It at east gives an illusion to the level of precision that is being claimed.
Figure 3: 6-D Point Precision incorporates all sources of error at any desired work location into a meaningful three-dimesional value.
Point precision
The language used can be seen to be deficient; it is not being refined enough and evolving quickly enough to help differentiate available motion-control solutions. So saying, Alio Industries has introduced the concept of Point Precision, which has now been adopted by NIST as the future standard methodology of measuring and quantifying motion systems.
Point Precision includes all six degrees of freedom of errors of each axis in motion, guaranteeing the precision point in the full work envelop. As an example, the Hybrid Hexapod has a 3D point precision of less than 100 nm repeatability anywhere in its full work zone. With that information a customer with, for example, a demanding metrology application can be extremely confident in the uncertainty measurement error quotient.
Point Precision allows for a “precision number” to be quoted based on an exact point on the wall, as if you used a laser pointer, whereas today’s standard only gives the measurement to the wall as if using a flood light. As a signifier of accuracy and precision today, Point Precision is beneficial for many applications from laser processing to metrology.
We have moved the conversation along, and in terms of specifications we have changed the language and now routinely talk about Point Precision, referencing performance specifications to a point in space, not the planar methodology current standards use. This is the basis of the new NIST standard for measuring motion systems.
While there are compensation methods to reduce error sources in conventional six-link hexapods, they do not improve performance at the single-digit micron or nanometer level. Motion systems’ straightness and repeatability performance must be analyzed and specified using a “point precision” methodology that accounts for all 6-D spatial errors in order to provide a true representation of nanometer precision, or what Alio calls True Nano precision.
There are numerous companies working in the area of micro and nano manufacturing that exist because of a passion to lead and to provide industry with solutions that stimulate innovation and advance the chances of achieving success in ever more exacting precision engineering applications. By their very nature, they push the boundaries and strive to provide technology solutions that facilitate greater and greater precision, which is consistently demanded across industry.
Alio has adopted a new approach to address the lack of clarity that exists specifically in the area of motion-control solutions. Through the process of education and redefining the language used to explain its technologies, Alio will give industry the tools and understanding to differentiate between the alternative levels of accuracy and repeatability that exist in the market today.
With the creation with NIST of the Point Precision as the future standard methodology of measuring and quantifying motion systems, Alio is exemplifying the uniqueness of its motion-control solutions in the area of nanometer precision.
ALSO READ: How to be gentle and accurate with linear motion
Sponsored Recommendations
Latest from Electromechanical
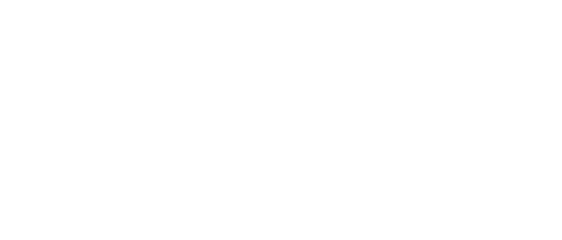
Leaders relevant to this article: