The future of laser control and its advantages in precision processing
This is Part I of a three-part series on laser processing with modular control. Read Part II and Part III.
Lasers have been used for welding and cutting applications in materials processing for many years. However, laser technology has frequently been considered a specialist area, requiring complex control systems for accurate positioning, as well as significant investment and expertise. Recently, the cost of lasers has decreased, opening this powerful technology up to new applications; even the latest extremely fast ultrashort pulse lasers are now feasible options for machine builders who would typically have used less risky laser setups. The commoditization of lasers means that system integrators must do more to gain and maintain an advantage, and that positioning and control, as integral parts of any laser system, are important elements of this. The newer technologies work in a slightly different way, so it makes sense that positioning and control also need to be different. The basic ability to fire the laser in the right place has become more challenging, and a simpler approach is even more important than ever, especially for those who are completely new to the technology. A uniquely modular approach to laser control makes it far easier and faster for system integrators to design and build systems in the first place, whether or not they have previous experience with lasers. The use of industrial control networks such as EtherCAT makes this modular approach even more flexible, as other items, such as sensors or non-motion devices, can be easily incorporated. Why choose laser processing?
There are many significant advantages to using lasers instead of traditional machining processes; not least is their capacity for much higher throughputs. Lasers are not susceptible to the same wear and tear that can lead to breakdown disruption and costs in mechanical components and are often efficient at processing materials that are otherwise notoriously difficult to deal with.
The fine beams of lasers also give a level of elaborate detail and accuracy that is nearly impossible to create using other methods, which is ideal for applications, such as those generating high aspect ratio holes or other features requiring similar high precision. High-intensity short pulse lasers, in particular, are incredibly precise. The low thermal energy deposition around the beam of these lasers means there is negligible damage to the surrounding areas.
Lasers can even process below the surface of a material, depending on where the beam focuses. Examples can be commonly found in microelectronics devices, such as light-emitting diodes (LEDs) and flexible displays.
Balancing speed, power and precision Whatever the application, fast shuttering and accurate firing of laser pulses is essential to ensure consistent, high-quality processing. Precise placement and energy control are crucial for this and can be achieved by linking the automation and motion system directly to the laser output.
It is extremely important to be able to make sure that the laser is focused on the right place for the right amount of time and delivering the right level of power in order to prevent damage to the material or the production of inaccurate parts.
One option is to link laser power to pulse rate and modulation. If the power is fixed, then the motion system will need to run at a constant speed to ensure that the correct level is delivered across the surface. This suits some operations, such as raster scans where the laser is fired following the motion in one direction or during the constant velocity phase between acceleration and deceleration phases.
It is important to remember that if the motion is badly tuned, jerks may result in bad processing. Poor placement accuracy could also create a bad quality part. This is a simple but effective process, for example, in welding.
Another approach is to precisely control the laser by pulse placement along the motion path, regardless of the vector velocity. It is also possible to combine these two methods to control scaling of the power output, which overcomes undesired features of the laser electronics or optic path.
There are several technologies available in the industry that can generate such accurate, high-speed, position-based events linked to electronic outputs, for example, laser pulses. Although subtly different from each other, they essentially do the same thing for motion in a single axis.
Some are better suited to galvo-technology; others are more aimed at motorized positioners. With the development of a modular controller, position event generation (PEG) is emerging as a way to link a laser to multi-axis positioning.
Challenges of multiple-axis control Paths that create three-dimensional trajectories can be created from three or more axes. Examples are simple dual-vector tracking—generated from two axes and widely used for linear xy table contouring, including circles or arcs and straight lines—a linear theta combination for processing tubing, or any combination of linear and rotary stages, for example, producing helical motion for drilling.
Until recently, controlling the motion path for lasers across multiple axes has come with certain limitations relating to performance, speed, practicalities and, not least, higher complexity and costs.
Restricted application, performance and speed Many of the drives available for precision motion and laser processing have to be predefined, depending on the feedback device used on the stages or the table used in the motion system. Positional feedback means a device that is capable of reading the stage’s position, but also allows the controller to calculate the speed of such a device.
Some motion stages do not use any feedback; they rely on the principle that the commanded motion request equals the actual response.
Typically, feedback systems are either incremental or absolute. Incremental encoders require a reference point or known position when the system starts up, often a homing switch. In comparison, an absolute encoder system has the positional data built into the feedback measurement scale. This positional data is available at startup and therefore removes the step of physically moving the system to a reference device.
Incremental feedback systems
A potential problem with a square-wave encoder occurs when it has a high-count output to obtain resolution and the system also requires high speed. The output frequency could potentially exceed the maximum frequency input of the controller’s feedback circuit, resulting in position loss. Sine-wave encoders are able to provide much higher resolution with higher-stage speeds because the controller inputs the data at the fundamental frequency of the encoder, which is much lower than the square-wave equivalent. The controller feedback circuit internally subdivides the sine wave into digital steps to produce the internal digital steps; this process is called multiplication. In practice, a square-wave encoder may start out as a sinusoidal encoder, and the key difference is where the digitalization or multiplication takes place—at the feedback device in the case of a square wave or in the controller.
However, many laser-firing controllers unfortunately cannot use sinusoidal feedback to produce an output that will trigger the laser; their electronics require digital square-wave signals, and this may limit their usability to low-speed systems with high-feedback resolutions or to high-speed systems with low-feedback resolutions.
Multiple feedback in multi-axis systems
Laser-synchronizing technologies use encoder data for single-axis-path motion to trigger, for example, one-to-one firing so that there is a single laser pulse with every millimeter or micron moved. When it comes to multi-axis, for example, pulsing in a circle, the same principle can be applied—data is taken from the individual encoders of each axis and fed into onboard electronics hardware, where the combined vector output is calculated.
This has been the accepted norm for many years, and, in theory, its accuracy comes from the fact that it is based on real-time positional information from the encoders. However, in reality, if the motion system is not adequate in performance, then this approach will produce poor results. For example, a constant-speed circle on an xy table is made up of sinusoidal changes in velocity for each axis. A change in velocity means there must be an acceleration associated with the motion. Acceleration is directly proportional to following error—the difference between the commanded path and the actual path. Therefore, the path will always deviate from what was commanded, and it is the user’s responsibility to ensure the error is below the threshold for the required accuracy. The path may be longer or shorter because of the deviation, which would mean the laser pulsing could be activated at incorrect positions.
Additionally, the electronic circuitry used for processing multiple feedback devices and creating the output vector used for firing can result in a significant delay, or latency, to the output; the more encoders that are tracked, the more dramatically the speed of the output reduces; consequently the data input rate, or tracking, of each feedback is reduced.
Non-incremental, non-direct or non-feedback systems
Firing hardware that requires encoder data obviously cannot be used to generate events for motors that have no feedback—for example, stepper motors. Similarly, they are not appropriate for serial-communication-based absolute encoders. These encoders do not need to be homed when they start up, which can be a significant advantage with regard to safety and convenience for some advanced systems.
Kinematic systems like hexapods are also challenging. The encoder data is not directly linked to the position or motion in a parallel direction or may be a combination of data from multiple axes that requires calculation and so does not generate direct triggering for paths in Cartesian coordinates. There are very few automation controllers that can handle this level of complexity to ensure that the motion system not only has the correct motion performance, but also the ability to read in and trigger out the encoders used for these applications. With this in mind, users should consider pulsing strategies that do not rely solely on direct feedback.
Whichever method is chosen, the machine builder should always consider the motion performance of the mechanics and controller. Motion systems have other system issues, such as resonances, low bandwidth, under-powered motors or mechanical inadequacies, including accuracy, roll, pitch, yaw, flatness, straightness and stacking areas, that need to be appropriately matched to the system requirements so the work piece or the laser head is in the right place when firing occurs.
Dr. Cliff Jolliffe is head of the automation market segment at Physik Instrumente (PI). Contact him at [email protected].
Sponsored Recommendations
Latest from Electromechanical
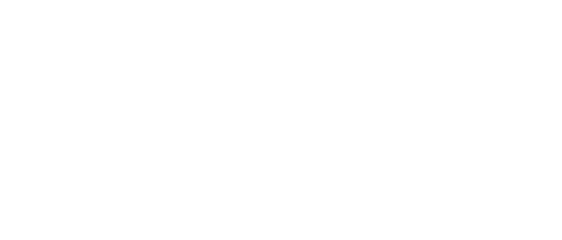
Leaders relevant to this article: