Can hydraulic pumps, actuators be controlled with the same PLC?
We need to add hydraulics to a newly designed module in our machine line, to move heavy loads relatively quickly and with precision. Can we control hydraulic pumps and actuators with the same standard PLC that we use for other machine control functions, or do we need to look into more specialized hydraulic controllers?
—from April '08 CONTROL DESIGN
ALSO READ: Hydraulic Systems Get Smarter, Less Noisy
Answers
Simulate Before You Execute
Basically a PLC can control hydraulic motion. It’s more a question of the dynamics and precision of the move which has to be achieved.
Especially if a position encoder is utilized to close the control loop electronically, the differences between a PLC and specialized electrohydraulic motion controllers are noticeable. For high precession digital technology and feedback SSI should be preferred. PLCs have, compared to specialized controllers, less performance with respect to sample time, I/Os and optimized algorithms to close the motion loop with high precision and dynamics. For example, the dynamic performance of a high-mass system can be optimized by a control feature called active damping. Here the acceleration of the motion is processed to stabilize the motion itself by compensating for unwanted disturbances. This a feature only provided by specialized motion controllers.
The beauty of specialized motion controllers is they can act as intermediate electronics to improve the motion performance. This means one can start to control the motion with a PLC and if the performance is not there, simply add a specialized electrohydraulic axis controller. This trial-and-error approach can be time-extensive though. Therefore it is recommended to consult a motion control expert with the capability to run a computer simulation of the overall system to make an engineered judgment before deciding which type of motion control is the best for the given application.
Michael Liedhegener,
Manager, development new technologies,
Bosch Rexroth—Industrial Hydraulics
Unacceptable Determinism
General purpose PLCs are fine for performing general control functions but can typically not control timing loops precisely. This is OK for controlling processes that are slow or not time-critical, but this lack of determinism is often unacceptable for precise motion control. By contrast, electrohydraulic motion controllers are designed to ensure that control loop timing is maintained precisely, even when moving heavy loads.
Further, the latest hydraulic motion controllers have the ability to control pressure or force as well as position, something that PLCs typically can’t do. Maintaining pressure control with heavy loads is something that gives hydraulics an advantage over using electric motors, but that advantage can’t really be delivered with PLC control alone. Since motion controllers can transition smoothly from controlling position to controlling pressure/force, they will be able to keep the motion of a machine such as a press smooth. In addition to promoting high-quality machine output with less waste, this also reduces maintenance costs compared to systems with discrete bang-bang hydraulic control.
New multi-axis motion controllers also support the synchronization and/or gearing of multiple hydraulic axes. This coordination enhances machine productivity by allowing machines to go faster without jams or missed steps. Maintaining complex relationships between the motion of multiple axes is extremely difficult or impossible to achieve with PLCs. The same applies with changing control loop gains on-the-fly as a machine runs. An electronic motion controller can do this, but it’s typically challenging for PLCs.
This is not to say that PLCs don’t have a role to play in hydraulic motion systems. PLCs still make sense for performing simple control or supervisory functions and for performing lots of I/O that is not timing-critical. Practically speaking, a best-in-class motion controller product will complement the PLC and allow each product to perform more optimally. Using a combination of PLCs and motion controllers often allows the machine builder to use a smaller, less-expensive PLC in the machine than would be required if the PLC were to do all the work.
Bill Savela,
PE, motion controller product marketing manager,
Delta Computer Systems
PLC-Challenged
Hydraulics are often seen as easy control systems, and indeed they can be in cases where precision and speed aren’t necessary —for example controlling a lift with a digital on/off signal without position feedback and utilizing limit switches to signal the end of the stage. Using a PLC in these basic hydraulic control cases is definitely possible.
[javascriptSnippet ]
However, positioning hydraulic cylinders with accuracy is challenging and can require complex control intelligence since hydraulic systems are non-linear by nature. For example, the dynamic behavior of a cylinder at its initial position isn’t comparable to the dynamic behavior of the cylinder when it is at the middle or the end position. This non-linear response requires applying complex PID algorithms such as gain scheduling, feed-forward and smoothing techniques to adjust control parameters depending on the shaft position. These types of advanced processing are challenging at best with a standard PLC.
Also, because there is a requirement on positional accuracy, these systems need to include analog measurements such as force feedback (strain, and magnetic stripe sensors (position) that standard PLCs struggle with since they’re not measurement class hardware. This usually adds another level of complexity to solving hydraulic control problems because connecting these types of sensors to a PLC requires separate signal conditioning or sometimes the creation of custom circuitry.
Finally, there’s the issue of speed. Control systems are only able to safely move as quickly as you’re able to close the loop in your PID algorithm. For hydraulic systems, this not only requires high speed analog I/O, but more powerful processors to handle the advanced algorithms fast enough to keep up with the speed of the system. For higher speed hydraulic applications it may be necessary to close the loop at rates of up to 1 kHz, which presents a significant challenge for standard PLCs when it comes to acquiring and processing analog data.
Where does that leave designers who are trying to integrate hydraulics into their systems? A number of vendors have built commercial hydraulic control systems that are based on PLCs with added hardware to handle more common hydraulic control challenges. These systems provide a good solution for hydraulic control. However, machine builders such as Euro Electronics and VAPO Hydraulics are turning to more customizable COTS hardware such as National Instruments' CompactRIO that integrates an embedded real-time processor with a user programmable FPGA to provide PLC reliability with PC processing power. With such hardware, they’re able to reliably control systems moving at up to 7.5 m/s or to position loads of up to 20 tons to within 100 µm.
So, can you use a PLC to control hydraulic pumps and actuators? Yes. For lower speed applications that don’t require precise movements, PLCs provide a viable option for hydraulic control. Is there a better tool for the job? Yes, especially as precise movements and higher speeds become involved. These types of applications require position or force feedback and advanced control algorithms, which challenge the capabilities of the standard PLC.
Arves Stolpe
Product marketing engineer
National Instruments
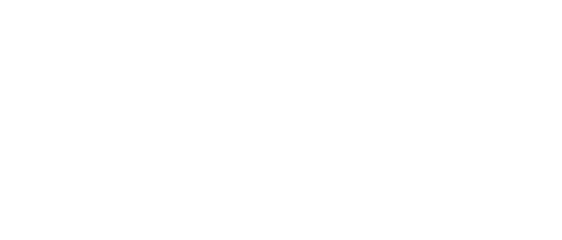
Leaders relevant to this article: