Knowing the maximum materials-handling throughput for an autonomous mobile robot (AMR) can help to determine the number of people who can be reallocated from materials handling to more valuable tasks. This is what drives the return on investment (ROI) of an AMR solution. Often, people will consider the top speed of the vehicle and make a throughput calculation, but there is a lot more that goes into throughput optimization.
There is a lot of engineering that goes into optimizing each element, but at a high level the formula is very simple:
Throughput = Payload * Average Speed * (1 - Downtime Percentage) / Round Trip Distance
The first two variables speak to moving as much material as quickly as possible. The third variable is about minimizing all the occurrences of events that make a robot unavailable to do its work. This includes the time the hardware is broken, the time the software is lost and robot-charging time. The last part of the formula, round trip distance is dependent on your facility and workflows, and it’s independent of the AMR technology.
Let’s look at each variable in more detail and consider the engineering elements of each.
When looking at an AMR, look at how much it can carry, but don’t forget to take into account the weight of attachments—for example, a robot that can carry 1,500 kg in addition to 400 kg of attachments like conveyors or lifts.
Next let’s look at agility and speed. The faster the robot drives on average, the more quickly jobs are done, the more jobs you can get from a single robot, the fewer robots you need, and the higher your ROI.
A lot of times people consider only the top speed of the robot. As best as we can tell, the highest speed is 2 m/s or 4.5 mph. But that doesn’t tell the entire story. Just like when people are walking, robots are often not driving at top speed because of the time they take to turn or dock, which often requires slowing down in order to maintain safety of people and equipment.
When multiple robots slow down in the same place, that leads to bottlenecks which cause backups and delay, so it’s really average speed that determines throughput. With more sophisticated sensors and smarter driving algorithms to help with turning and docking, average speed can be increased dramatically even while keeping top speed capped (Figure 1).
Figure 1: This real-time video shows the Otto 1500 safely making a tight turn at speed while carrying a 1,900 kg loaded.
The charts in Figure 2 show the aggregate effects of many robots driving with maximal agility and the difference smarter driving algorithms can make. This is a before-and-after case for some work we’ve done.
Figure 2: The charts show the aggregate effects of many robots driving with maximal agility and the difference smarter driving algorithms can make.
These two charts show average speeds in each location on the map, lighter colors being faster. You can see that the new technology on the right is much faster at the turning points than the graph on the left which has older driving technology. The result of this difference is 60% more throughput from the same fleet doing the same workflows in the same facility.
The two charts in Figure 3 show the distribution of robot speeds over time. As you can see, both show a top speed of 2 m/s. No one would really want to go any faster than that in an environment with people. But, in the bottom chart the median speed is almost 1.5 m/s, much faster than on the top.
Figure 3: The two charts show the distribution of robot speeds over time. As you can see, both show a top speed of 2 m/s. No one would really want to go any faster than that in an environment with people. But, in the bottom chart the median speed is almost 1.5 m/s, much faster than on the top.
When considering an AMR, don’t just look at top speed, ask about average speed and the distribution of speeds for representative workflows. This sort of analysis can ensure that you get what you expect in terms of throughput and ROI.
Moving a lot of material quickly is not enough. You need to minimize the amount of time the service is interrupted. This is critical because stationary robots don’t deliver ROI. The first thing we need to talk about is reliability.
Consider the construction of the robots, what kind of punishment they can take and their fitness for industrial environments. For example, with metal frames and skins, some AMRs can take hits from forklifts at full speed and return to service just fine.
The reliability on the inside is just as important. Ask about mean time between failure (MTBF) and how that’s calculated and proven.
When things do break, as they sometimes will, the vehicle needs to have great diagnostics so that the time to diagnose is low and great design for access so that time to repair is minimized.
Ask about triage and diagnostic tools so you can get an idea of how long it will take to diagnose problems and then figure out what the time to repair looks like. How long does it take to pull apart a robot, replace parts and put it back together again? For larger robots, how many people does that require? A photo similar to the one in Figure 4 can demonstrate modularity for repairs.
Figure 4: A photo similar to this one can demonstrate modularity for repairs.
Another key element of uptime is minimizing interventions and making sure that the robots don’t get lost, especially in facilities with repeated features or a fluid landscape. Make sure you ask about localization capabilities and mean time between intervention. One feature to highlight is remapping zones, which allow operators to highlight areas that are likely to be rearranged so the AMR knows to update its map its next time through. This enables the robot to localize to the new setup without losing its global position.
The few points are about avoiding blockages in traffic flow. It’s important to ask what sort of features are available to avoid blockages.
While it would be amazing if all factories were built for AMRs from the start, we know that’s not the case. Some will have unfortunate choke points that have the potential to bring traffic to a halt. AMRs need features, therefore, to ensure that they can defer to one another intelligently and travel fluently through bottlenecks. Ask specifically how the robots will handle the most challenging places in your facility. In Figure 5, you can see how an AMR can use elements like one-way zones, queueing points and a traffic-light feature to coordinate traffic and make sure that robots flow smoothly through this choke point and wait patiently in a prudent location while its peers pass by.
Figure 5: An AMR can use elements like one-way zones, queueing points and a traffic-light feature to coordinate traffic and make sure that robots flow smoothly through this choke point and wait patiently in a prudent location while its peers pass by.
Another way to prevent blockages is to simulate your environment and design your process flow before you buy or deploy your first robot. This is important for a deployment of any size because you want to make sure you get the right number of robots before you start and know that they will be sufficient to get the work done. You don’t want to be surprised later with the need to buy more robots.
With simulations, you can cheaply execute not just one run of the workflow, but hundreds of runs. You want to make sure that it doesn’t just work at 9:00 am, but is also going strong at 2:00 pm and not subject to cascading backups that bring the deployment to a halt.
You also want to inject faults to stress-test processes and make sure that traffic keeps flowing even when there is an unanticipated problem with a robot or an unexpected persistent obstacle. Simulation is key to rightsizing your deployment and keeping throughput and ROI as high as possible since it’s impossible to do these tests live without disruption.
Another key element to uptime is charging. It’s critical that robots don’t run out of charge and stop on the floor. Ask questions such as:
- What is the battery capacity?
- What is the charge time for the battery?
- How many charges can the batter take over its lifetime?
Also, find out how charging is done:
- Is it manual, or does the AMR charge itself?
- Does it need to be scheduled as a job?
- Does the fleet management system coordinate charging for you without any effort on the part of your operators?
You may also want to ask about advanced charging features. For example, an opportunistic charging functionality optimizes charging by finding opportunities to top off charge a little bit at a time, rather than letting it drain all the way down. This reduces risk of the robot running out of charge and blocking the work. It also means less wear and tear on the battery.
Conclusion
Think about hardware, software and services to get the highest possible throughput and ROI. Some companies will choose AMRs based on many other factors besides the ones that impact throughput. Hopefully, whatever and whoever you choose, your decision will be based on information that positively impacts ROI as you plan this critical purchase decision.
ALSO READ: Hey robot, want to go for a stroll?
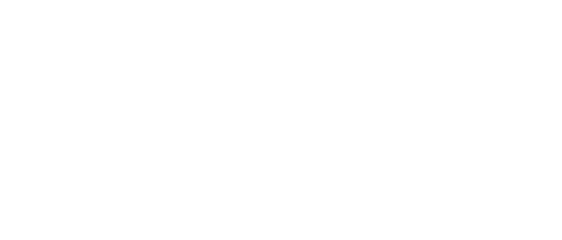
Leaders relevant to this article: