We have been designing and building machines with robots for about 15 years at Richlin Machinery, in Farmingdale, New York, but the lay of the land for robotic automation is changing so quickly now. Because of that, our role in the process is different. It used to be that the robot may cost $50,000, and we as integrator were quoting three to four times that capital expense to complete the project. Safety guarding, as well as difficulty in programming and interfacing, is fading away with the introduction of products like those from Universal Robots (UR).
Now our responsibilities are different; it's a whole new world. Instead of doing four or five automation projects a year with robotics, we are now on our 16th robot as of June 2017 and are on track to double that by year’s end. It's a different game. We charge a lot less, and we don't have as much to do. Get in, get out, and move to the next one.
A good example of this is a machine-tending application we worked on with Lowercase, located in Brooklyn, New York, and one of the few American eyewear manufacturers. Lowercase needed a robot to replace the machine operator. For this application we also partnered with Axis New Jersey, a high-tech distributor of Universal Robots and Robotiq (Figure 1).
Figure 1: Robotic machine tending is a good place to start with automation in a small manufacturing operation.
(Source: Robotiq)
Made in America
American eyewear manufacturers were all bought by foreign interests in the 1980s, stopping the domestic production in the process, so most American eyewear brands are made overseas. Two years ago, Brian Vallario, an architect, and his friend Gerard Masci, a finance worker, decided the time had come to bring back something that was long gone in the American eyewear industry: the “Made in USA” label (Figure 2).
Figure 2: A wide variety of eyeglass frames can be manufactured on the automated equipment.
(Source: Robotiq)
Vallario and Masci started Lowercase. From the beginning, automation offered low production costs, while guaranteeing high-quality frames. The main challenges of the 1980s became the opportunities of today. The company’s vision was to have full control of the product and deliver high-end quality, even with as small of a production as theirs.
Before launching Lowercase, Vallario specialized in digital fabrication in an architecture firm. Although he didn’t know much about robots, he was aware of the benefits of automation. “I had done a little bit of research on robots when I was in graduate school, but I never really had any working experience with them. It was a complete learning process but it went fairly smoothly. With the help of Axis New Jersey, we were put in touch with an integrator but the majority of the integration was done on our own.”
At Richlin Machinery, we work well with the robot manufacturers and distributors who refer customers and applications to use, as they did with this Lowercase project. But we find about half of the projects ourselves. At the beginning of the project Lowercase came to Richlin, recommended by Cynthia Kradjel at Axis New Jersey, a high-tech distributor. They had decided which machine tool to purchase but had not worked out the end-effector tooling, work-holding fixtures, integration or interface to the CNC machine tool.
How to get into automation
"We often run into customers who want to do automation projects so we work through their technical requirements, as well as their budget and timing," notes Cynthia Kradjel, an account manager with Axis New Jersey (www.axisnewjersey.com), a part of Power-Flo Technologies. "From the variety of solutions we offer, we try to put something together for them that will work."
Automation historically has been making a product, maybe a million units a year or even a million in a day, so an investment in automation was obviously required, and money was available to do it, explains Kradjel. "That's the traditional automation," she says. "Today, I cannot just go knock on the doors of 50 new factories that are being built in my region. That doesn't exist. In my region, many factories are being shut down, redeployed or repurposed."
One of the things Kradjel runs into in the New York area is that there are not many if any companies building new factories out there. "As a result, we work with smaller manufacturers and on smaller projects, or we modernize existing manufacturing applications," she says. "There are not many projects out there where the end user needs 100 robots and significant high-end automation. They need one robot."
What Kradjel finds is the end user wants to get into automation but doesn't have the economy of scale in production to get into the traditional type. "However, with a collaborative robot and use of certified peripherals with pre-written drivers, it's quick for users to connect the pieces," she says. "It takes away a huge barrier to entry for companies that don't have mass production."
The need to automate
Lowercase, a small startup company, follows this trend of small manufacturing and small automation projects. "Lowercase came to Axis New Jersey with a need to tend their eyeglass CNC machine," explains Kradjel. "Lowercase claims they are the only eyeglass-frame manufacturer in the United States. To do this, they must be efficient. What makes the application cost-efficient is the ability to use the robot to tend the machine (Figure 3)."
Figure 3: Lowercase had the need to automate to efficiently manufacture eyeglass frames and robotic machine tending made it possible.
(Source: Robotiq)
This is a case in which there is a clear justification for automation but no need or ability to purchase it large-scale. "What we recommend for cases like this is: Don't re-invent the wheel," says Kradjel. "We recommended Universal Robots because it has a collaborative robot that can work side by side with the operator; there’s no cages or guarding needed. The customer is able to set it up to do jobs and work around it at the same time."
Perhaps more importantly for these types of firms, especially in fashion and similar industries, is things change quickly, says Kradjel. "One day you are making one type of product, and then, one month or three months later, a different product is hot, and the production process must be adjusted," she says. "With Universal Robots, the users can re-deploy the robot relatively easily without a large integration project required."
Kradjel said large manufacturers are pushing the factory of the future and Industry 4.0, going from CAD to SKU, where just one unit is produced. These are all trends that smaller companies want to jump on, as well. They are looking for ways to keep up with the way manufacturing is evolving in a way they can afford.
When Lowercase looked at traditional robots, the integration costs were up to five times the cost of the robot, but, working with Richlin Machinery, the costs were equal to or less than the cost of the robot. This allowed Lowercase to proceed with the project, says Kradjel.
Tend to requirements and a design
Our firm, Richlin Machinery, launched in 1978, survives because we are always learning new skills, new products, new content and new techniques. We are a small custom machine builder and integrator, but, everything we do, we do in-house, except sheet metal and power coating. We're a jack-of-all-trades when it comes to machine building and automation, and we like the idea of modernizing and simplifying the integration process.
Leveraging Richlin's experience with machines and machine tending in this Lowercase project, we started with the requirements of work-holding in the machine and then laid out how the system would flow—staging parts, how parts are placed in and out of the machine, part turnover.
Workflow of getting the parts in and out of the environment is another task. At Lowercase, it was just a matter of building a table with appropriate fixtures that the end user could stack parts in and then walk away for a while. More commonly, we design infeed and outfeed systems to enable the robot to run much longer periods of time. In many cases it can be directly controlled by the robot with up to 16 inputs and 16 outputs available. PLCs are added as the complexity increases.
With the process flow worked out and agreed to by Lowercase, we provided some design and modeling services in Autodesk Inventor. This included a nesting system that staged the raw material in stacks. We created 10 to 15 part high stacks in a four-by-four array. The stacks were easily adjustable for different size eyeglass frames.
Where to mount the robot, robot reach and load handling were also reviewed. Everything we do is modeled first. We can visually check the robot reach and end-effector capability to confirm it all works as a system. This modeling actually starts during the sales process and doesn't complete until drawings are updated to as-built status.
Machine-tending details
To pick from a stack of parts to be processed, a Robotiq end effector was used. The grippers were electric and interfaced directly with the UR robots (Figure 4). We made some 3D-printed jaws that created a capture surface to reliably handle the part. The robot approaches the stack of parts from above and can press against the stack with up to 10 Newton of force. An optional force sensor, included as an option with the Robotiq gripper, sensed the part was engaged, signaling the gripper to close. As part of this quickly developed robotic pick-and-place process, a de-stacking routine, provided with the robot, was used.
Figure 4: The gripper was designed to quickly integrate to the robot with wiring, configuration and programming, requiring minimal work, engineering and programming to get it all up and running.
(Source: Robotiq)
"The Universal Robots stack/de-stack routine is part of its programming wizards, along with palletizing, conveyor tracking and force control," explains Brian Kobus, tech supporter at Universal Robots (www.universal-robots.com). "What we call wizards are pre-written programs that only require minimal information to be filled in, such as setting a few waypoints and setting parameters specific to an application. The wizards make common applications very easy to program with Universal Robots. They show a few lines of code on the teach pendant, but in the background more in-depth script code is used to simplify this complex program."
Close door and press button
The robot interfaced to the machine tool, picked and placed product and blew off the tooling and nest for cleaning purposes. To simplify integration, the robot also pressed the cycle start button on the CNC machine's HMI panel.
A robot-controlled solenoid was added to control the opening and closing of the CNC work-holding fixtures. Once the robot placed a part, it actuated a dual-position, detent valve to clamp it in place. An air pressure sensor was also added and monitored, and the robot stopped everything if air pressure was lost. It was also necessary to blow out dust from the fixtures, so a nozzle was added to the robot end effector and connected to a second solenoid controlled by the robot.
The robot also closed the CNC machine's door. With some CNC machines, there is no easy way to tell the machine to cycle start other than to press the cycle start, which the robot did in this case, using a gripper finger. The CNC machine would then machine the part and signal completion, via a digital output, when the cycle was complete. The robot would then open the machine door, grab the finished part, open the part fixture and then move the part to a finished part bin.
Tend safely
Richlin also provided integration of the safety where needed. Not all collaborative robot applications can be deemed safe. In other cases and commonly, even though the robot is collaborative and won't hurt anyone, management requires light curtains and safety mats.
We perform a safety audit as part of our process. We share with the customer that from our experience and by following the guidelines for a safety audit, this is the recommended safety design along with what not to do. Beyond that, a third party can certify the safety system.
Simplified automation
"I talk with really smart people all the time," says Axis New Jersey's Kradjel. "They don't always have to go the complicated route. Sometimes it is to their benefit to go with preconfigured, certified options instead of reinventing the wheel."
It's a similar concept with the Robotiq gripper, continues Kradjel. "Instead of the customer purchasing a new gripper with fingers and sensors, designing the mounting bracket and programming code necessary to open and close the gripper, Universal Robots created a platform called Universal Robots+ to simplify integration," she says.
A Robotiq RG2 gripper is an example of a preconfigured, certified plug-and-play option. It includes a two-finger adaptive gripper, and a force-torque sensor can be added between the gripper and robot, as well as a vision system. All the items are interchangeable, some or all can be used.
"Robotiq grippers are part of Universal Robots+, a platform that offers plug-and-play products certified to work seamlessly with UR robots," explains UR’s Kobus. "UR+ integration means that the software controlling Robotiq's gripper has been implemented directly on the UR teach pendant, so both robot arm and gripper can be easily programmed through the same interface."
This UR+ concept allows us to focus on delivering the best cobot on the market while working closely with third-party developers to ensure that our partners and end users can deploy quickly by choosing optimized UR+ products, continues Kobus. “It is a shared business value model that we extend to our sales channel partners," he says.
"Save time in the deployment by having things that can quickly connect to the robot that has already been tested and certified," says Kradjel. "To the universe of people who have not worked with automation, it seems very daunting. How are we going to implement it while running the business? The big integration projects will just never happen in many factories. It's making automation more accessible to companies who wouldn't normally have the resources or time to do it otherwise. It is also making it re-deployable."
Entry-level automation
All of the code for the interfacing and controlling program was written in about an hour. This highlights that the cost difference of what it used to be and what it is today is huge. With two days on-site, the mechanical hardware was installed, the robot mounted and the interface to the CNC machine was worked out and running. We spent another day on-site while the customer worked through the system.
ALSO READ: The keys to robot selection, safety and collaboration
The integration of the robot to the CNC machine took only a week and is a success. “Overall, we think the solution is flexible, easy to redeploy and cost-effective, compared particularly to industrial robots, which require caging, and, once they’re integrated, they need to bring an integrator back to make any changes,” explains Kradjel. “In the case of Lowercase, we helped to train them, so they’re able to program the robot and keep it current with what they want to do on a daily basis.”
Without seeing life through a pair of pink glasses, Lowercase’s Vallario and Masci definitely see great things coming for Lowercase. Automation is an important part of many of their future projects, not only regarding the addition of new robots in the factory, but also to raise the number of hirings. "A collaborative robot is operating our CNC machine, but we’re not hindering jobs,” says Vallario. “Automation just creates different jobs. Right now, we’re not looking for someone to operate a CNC machine, but we are looking for engineers and designers who can work with robotics to improve processes. If that helps us to grow as a business, that helps to create jobs.”
And even though Lowercase’s co-founders do not think that eyewear production could be fully automated just yet, they see many other opportunities to bring more robots into their team. “As we grow, we are definitely looking for new ways to automate our processes," adds Vallario. "There are many time-consuming steps involved in manufacturing a pair of glasses that require delicate handwork. We’ll never be able to automate everything, but there is a lot that can be done and we’re looking forward to it.”
At Robotiq, they like to say, "We free human hands from repetitive tasks." They also make it easier to install robotic automation. This makes it simpler to be made in the USA.
Sponsored Recommendations
Latest from Robotics
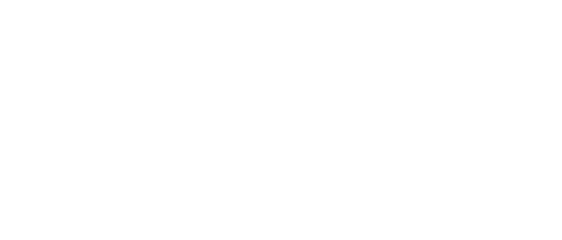
Leaders relevant to this article: