Compliance for robots in collaborative and other applications
Roberta Nelson Shea, chief technical compliance officer at Universal Robots, will be giving a presentation on safety implications as part of the Collaborative Robots: Opportunities and Challenges session on April 4 from 10 am to 11:30 am at Automate 2017 in Chicago.
Nelson Shea responsible for product safety and reducing barriers to global acceptance and deployment. She has spent more than 35 years as a professional within the field of manufacturing automation, 23 of them additionally chairing the U.S.-American National Robot Safety Committee (ANSI/RIA R15.06). She has also been elected one of the top 100 Women in Safety by the American Society of Safety Engineers (ASSE). As convenor of the committee ISO/TC 299 WG3 (ISO/TC 184/SC2), she led the introduction of ISO/TS 15066, which, as an extension of the established ISO 10218, is the first document defining standardized safety requirements within human-robot collaboration. Contact her at [email protected].
Compared to traditional industrial sectors, robotics is a relatively young field with only about 40 years of deployment history in workplace environments. Technology within this field however is advancing incredibly fast, and thus compliance needs to adapt to keep pace with these rapid changes. Another challenge is how to convey the myriad facets of compliance comprehensibly to end customers and integrators for issues such as knowing when a robot system is really compliant or what the requirements to which the robot and robot system have to comply are.The first thing, which has to be clarified for the topic of compliance, is always in what industry and for which purpose the robot system will be used. Compliance requirements differ from application to application. For example, there are requirements for EMC thresholds, temperature, indoor/outdoor, expected people—workplace, public, children, elderly, disabled—performance or accuracy and work environment. The robot is the arm or manipulator with its controller, while the robot system is the robot plus the end effector for the intended application or use. For other work environments, such as electronics, pharmaceutical or food processing, there could be additional requirements, such as cleanroom use or washdown.
ALSO READ: Applications that will benefit from collaborative robot innovations
Depending on the application and industry, there are very different expectations. This is also true for compliance in a safety context, especially when it comes to cage-free human-robot collaboration without additional safeguards (Figure 1).
Figure 1: Collaborative robot arms operate with no safety guards at FME Feinmechanik in Buchberg, Switzerland. “The combination of flexibility, easy programming and the fact that the robots can work directly with my employees without bulky safety housing were the factors which persuaded me to invest in this technology," says the company's CEO Marco Botolan.
Challenges for compliance in robotics
As the robot arms are mounted in many different ways—for example, to a wall, upside-down or on top of a table or mobile platform—and equipped with various end effectors, the manufacturer faces further challenges: Will the robot system remain compliant for collaborative and cage-free use after the addition of end effectors and parts?
First, some questions need to be answered. The parameters needed—payload, reach, performance, for example—have to be clarified for both the robot and the additions that make a robotic system. From a compliance point of view, many different additional factors exist when a cage-free collaborative application is desired. All of these need to be taken into account. A risk assessment is required to make the robot application (robot + end effector/part/other equipment) compliant to safety standards and technical specifications, such as ISO/TS 15066.
Furthermore, manufacturers need to be precise in their communications with their customers and partners. Robot manufacturers can only guarantee the compliance of their products to their specifications and approvals. These can mean that the robot is accurate to the tenth of a millimeter and the robot arm complies to be used in accordance with ISO/TS 15066 including Annex A. This Annex A covers a range of force and pain threshold values in which a collaborative robot system can be used without guards and protective devices. Often, the application can be collaborative without cages and protective devices; however to do this could mean that the speed is limited and this speed is insufficient for the needed production rate. In this case, typically a safety scanner is then used to allow the production-rate speed when no one is nearby and the acceptable reduced speed when personnel are close to the robot system.
As a manufacturer, we do our utmost to inform our distributors and end customers about the intended use as comprehensively as possible. However, robots are being used in many different sectors, so we cannot cover all the applications that partners and end customers might develop.
Who is responsible to test for compliance? Manufacturers worldwide do their utmost to ensure compliance of their products to the intended use and to as many use cases as they can envision, if reasonable. However, just as robotic technology is ever advancing, so is the ingenuity of integrators and end users. Therefore, as inventive integrators uncover unprecedented ways to use and develop robot applications, they have to ensure that the complete application complies with applicable requirements. For cage-free collaborative applications, these requirements depend on the robot’s work environment, force values, shape and weight of the end effector and part and the maximum permissive speed of the robot to remain within selected pressure and force values.
[javascriptSnippet ]
Common ground
For clamping or quasi-static forces, testing is easy. In addition, clamping situation should be eliminated except for right where work is being performed. However, there is no unified means to test whether an application meets the free-space (transient) values, with many developing their own testing methods. There has been inappropriate transient testing using load cells, which simply replicates clamping (quasi-static) testing. There have been videos posted to the Internet that are robot performance testing, rather than testing safety configurations. Unfortunately these errors contribute to misleading both the public and users interested in collaborative applications.
Obviously, this confusion has resulted in different forces being measured. Thus, differences can arise in determining the appropriate limits at which each robot system should be configured so that the application can be deemed a cage-free collaborative application. Therefore, compliance managers need a common and comprehensively accepted tool to measure and simulate the quasi-static and transient contact values for a given application speed. These are some of the next challenges for standardization to aid in the compliance collaborative and cage-free robotics technology.
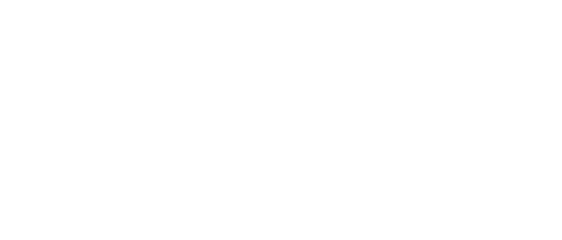
Leaders relevant to this article: