Evan Gonnerman, portfolio manager at Concept Systems, a CSIA-certified system integrator headquartered in Albany, Oregon, and CEO Steve Strong will present “Exploring Modularity in Robotics Work Cell Design" during A3's Automate Show in Chicago's McCormick Place on May 9 at 8 am. Contact him at [email protected].
Factory automation and industrial robotics have traditionally been developed as pinpoint solutions to specific applications. While highly performant and reliable, these systems are often difficult to support, intolerant of faults and nearly impossible to modify.
While the system-integration industry has embraced standard interfaces at the component level, it is rare to find standardized system or factory-level interfaces that are robust and reliable. By implementing an architecture that utilizes modularity as a foundational element, it is possible to deploy a system that does not compromise on performance or reliability while at the same time is dramatically more efficient and lower risk in the development stage.
Central to this modular approach is the robotic motion platform. This element of the system acts both as a functional block and as a connection to peripherals. The specific implementation of that motion platform can be abstract. A six-axis industrial arm, automated guided vehicle (AGV) and humanoid robot all can perform relatively similar functions, depending on the requirements, and can be controlled through common interfaces. Other modules at a similar level of abstraction to the motion platform could include:
- perception including machine vision, traditional sensing technology or data from a digital twin
- user interfaces, such as a human-machine interface (HMI) or pushbuttons, to allow for collaboration and external control
- tooling that enables the robot to physically interact with its environment
- safety that properly constrains the system from posing hazards to personnel
- cell control and supervisory control and data acquisition (SCADA) that receives and reacts to work-cell and environmental/factory-level data
- operational technology (OT)/ manufacturing executive system (MES)/analytics platforms capable of recording and communicating historical data
- recipe management that allows for off-line creation and analysis of system behavior
- off-line and real-time motion planning based on system state and sensor feedback
- artificial-intelligence (AI) and machine-learning (ML) algorithms.
All too often, the development of robotics tangles peripherals together to create a complex infrastructure that is rigid with highly restrictive limitations and capabilities. By separating peripherals to act as modules that tie together through known interfaces, robotics can truly be transformed into dynamic tools to change manufacturing and logistics environments (Figure 1).
There should be obvious indicators of a system developed with modularity as a foundation. When followed, these tenets ensure that the system will behave reliably and in close alignment with the design requirements.
Distinct functionality: Modules must be created to have a distinct function that, when called upon, will perform that task with reliability and repeatability. A core principle of modular design theory is the basis of trust in a module to perform its requisite task such that additional layers can be built without changing the base operation.
Interface design: In order for modules to interact and form a whole system, interfaces must be defined to guide interoperability. Modularity depends on strict adherence to the interface definition and trust in the completeness of that definition. Designing a modular system should begin by understanding and defining how modules will interact and the expectation of performance of those interactions.
Standard definition: A standard definition for what a module can and cannot be is required to properly validate and verify a system’s functionality. The definition allows for core functions, interfaces and complexity limits to be maintained during development and across teams. With standard definitions in place, development of modules and systems comprised of those modules becomes a reality at scale.
Platform approach: A platform approach allows for defining the context in which modules will interact and perform their functions. The platform defines the basis for which modules will lead operations and which modules will respond to lower-level commands (Figure 2).
Modularity, as it relates to robotics, can be implemented to separate a specific application from the core functions of the robotic system. For example, a palletizing robot may be responsible for taking cases of finished product from a machine and stacking them in a pattern on a pallet. By deconstructing the application from the system, it is possible to break a palletizing robot into the following modules: a robot for moving cases, a tool for handling cases and a motion profile to define stack patterns.
In a completely different-looking automation solution that involves a robot tending a CNC machine by picking parts from a fixture and placing them within the machine, deconstruction of modules can be done. The breakdown results in a robot moving machined parts, a tool for handling parts and a motion profile to define the method of machine interaction.
By looking at these examples, among many others, a trend can be formed that demonstrates any robotic system can be broken into modules that uniquely constrain the scope of functions that are performed (Figure 3).
The benefits of modularity in robotics are immense. Similar module structures allow for a common look and feel for training and maintenance of a system. This technological ecosystem of physical and software design reduces the requisite skill level to optimize machine performance, as well as scale new automation equipment into new processes. Because a modularized robot design has been taken, analytics and data patterns can be standardized across a plant floor, regardless of the application being performed. This allows for a production-level system design and has the ability to identify bottlenecks and utilize artificial intelligence to improve existing processes specific to a production space.
Modularity in design provides a basis for development that can be iterated. Instead of building an application from the ground up, modules can be combined to form a basis of functionality, and process-specific design considerations can be implemented to provide value on a case-by-case basis. The result is a faster time to production of automated systems with an allowance for higher-quality systems due to heavily tested and vetted module functions and operations.
On a practical level, modularity in robotics disassociates the implementation from the function. A tool that can handle a tote by an industrial six-axis arm can be deployed on a humanoid system. The interface for a peripheral conveyance section on an end-of-line palletizer can be deployed on a mobile robotic platform for interfacing with end-of-line finished pallets. A palletizing system that has hard guarding with safety hazard mitigations of light curtains and door interlocks can retain the identical modular functions while transferring the safety mitigation to be a collaborative robot capable of working together with operators. By designing a physical and software architecture that is modular in nature, the scalability, maintainability and dynamic capability of the system is dramatically increased (Figure 4).
As the world transitions to the mass adoption of artificial intelligence in business practices and realizes efficiencies in areas that previously relied heavily on skilled labor, standardized data sets in automation environments have never been more necessary. Modularity in design of robotic systems brings the ability to scale production environments, continuously improve existing processes through data-driven and AI/ML-assisted optimization and standardize technical skill requirements associated with operating and maintaining machinery.
A shift to configurable modular robotics from custom automation, brings value in the form of higher return on investment (ROI), lowered time to production for new installations and a higher level of quality due to the technical backbone established through well-tested automation modules in a system.
Finally, modularity in robotics allows for development of applications in robotics that carry complexity beyond the ROI justification, including welding, assembly and painting. Modularity has been a pillar in the rise of software-as-a-service (SaaS) offerings in the past decade due to reducing the barrier to entry for developers who have identified a need in the market and have the open-source tools to address that problem in the form of software libraries or modules. By taking this approach, modular robotic design can be the cornerstone for democratizing robotics.
Sponsored Recommendations
Latest from Robotics
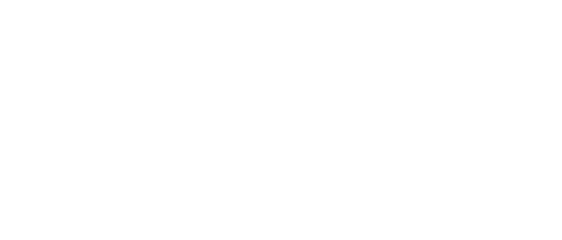
Leaders relevant to this article: