Distillery control system designed by university team reduces manual operation time
What goes into crafting and upholding the unmistakable taste of your favorite spirit, time and time again? A group of electrical and computer engineering students at the University of Colorado—Colorado Springs (UCCS), working as a team named Still Standing, got a flavor for that process and a taste of success when they designed and tested an automated still controller for their senior design project.
When a local craft distillery was interested in adding automation to its operations, the team was able to design and implement a novel control system for the distillation process. Ultimately, the control system was able to reduce the amount of time an operator had to be involved in the process and helped improve the overall quality of the product.
Understanding the challenge
Like every good engineering project, this one began with a problem. In craft distillation, small variations in the process that are not readily managed can lead to a disruption in the flavor profile of the final product. Manual control of the craft distillation process is tedious, time-consuming and prone to variation. For smaller establishments, any investment in automation must be economical and easily justified. Fortunately, a great selection of quality, cost-effective controls and instrumentation are now readily available and designed specifically for these types of applications.
The Team Still Standing began its work with an engineering specification agreement. The specification detailed requirements defined by the master distiller and included safety requirements, a range of environmental variables, control and operational requirements and integration preferences. Perhaps most importantly, the resulting system had to be easily adjusted by the master distiller.
The goal was to produce a working prototype of the craft distillation process utilizing automation that could be tested in a pilot setting and later scaled up. A piping and instrumentation diagram (P&ID) was generated, controls and sensors were evaluated, and, after a concept review with the master distiller, design work began.
Crafting the design
The prototype system incorporated both a data-logging capability and a notification-alert system, and it adhered to all safety protocols specified by the master distiller and industry standards. The AutomationDirect ProSense line of sensors coupled with the Productivity 3000 programmable logic controller (PLC) and C-more human-machine interface (HMI) were chosen for this project to demonstrate the viability of a mid-budget control system for craft distilleries (Figure 2).
This prototype system utilized the ProSense temperature, pressure, and liquid flow sensors, which included a user-programmable detection range, a valuable feature for this project. This is ideal for applications that are sensitive to small temperature variations, such as the distillation process, allowing the designers to zoom in on a small temperature range of interest.
The PLC development environment was ideal for executing this system architecture, and team members needed only minimal startup learning. Within the program tree are several organizational tools that made implementing the finite state machine simple and straightforward.
Elements of real-time data display were needed for operation and tuning, while data logging would be valuable for post-process analysis. The system was designed to display sensor data, operating state and any errors detected via the HMI, which also included USB storage capability. Both the PLC and the HMI worked seamlessly together and were configured with easy-to-use free software.
Feedback and visualization
The HMI display mirrors the state of the controller, updating screens based on the current process state. In addition, operators have the ability to alter process parameters via the touchscreen interface and view the system response in real-time. With a large display and color background, the HMI made it easy to observe, command and fine-tune the system (Figure 4).
Operators appreciate that the HMI can be viewed from a distance, which is an important feature for scaling the prototype to full production mode. A light stack and audible alarms were incorporated to provide additional system feedback.
Keeping the temperature in check
Typically, small batch distillation is performed by controlling the power delivered to the boiler, often in an open-loop method with no feedback. For increased purity, some distilleries choose to use a reflux still. Reflux occurs when a portion of the vapor is condensed and sent back down the column to interact with the upcoming vapor.
Reflux stills are particularly sensitive to environmental variations and require constant attention from the operator. Adding to the challenge, reflux often exhibits a non-linear response to temperature variations. During the distillation process, the vapor temperature at the top of the column will only change 5° from start to finish. All process temperature measurements need to be resolved to a fraction of a degree.
To address this concern, the temperature sensors were re-programmed to have increased sensitivity for their respective applications and measurement ranges of interest. By monitoring the process temperatures, pressures and flows in real time, the automated prototype system was able to maintain the process more responsively and with better resolution than was possible with only manual intervention.
Testing and validation
Testing was categorized into hardware testing, software testing and system testing to prove viability of the prototype, operational status and safety. A number of automated and manual tests were conducted to verify each specification requirement was met and the overall system performed as desired. Automated testing involved a virtual run of the system while simulating sensor values for temperature, flow and pressure. The Productivity Suite computer-based software was a key part of the testing process and provided valuable insights into system performance as the transitions between various states occurred.
When it was time to complete a test run on the still, the system was engaged, was put into idle state, transitioned to warmup and completed a fully automated distillation run. For development purposes, the team worked to distill isopropyl—rubbing—alcohol instead of ethanol. After starting with an alcohol concentration of 12%, the system produced an error-free run with a distilled product reaching the target 91% concentration.
Last call
For pilot projects like this, the PLC and HMI automation platform is important, but the primary focus is on developing and optimizing the process. The team appreciated how easy the selected automation platform was for them to learn and develop and how capable it was in operation.
Each part of the prototype system was designed and selected to be suitable for both the prototype system and the distillery’s full-scale production. Therefore, the prototype system was easily scalable to modernize the distillation process at the craft distillery. With the new PLC/HMI automation platform, the system was able to control the still and provide superior regulation of distillate quality. Ultimately, all customer requirements and specifications were satisfied, and the project was considered a success.
The UCCS ECE Department, Fall 2022, Team Still Standing is Benjamin Sprouse, BSEE and co-Founder F&S Industries, Matthew Scally, BSEE, Matthew Lake, BSCE, Cooper Tedstrom, BSEE, and Nicholas Eckley BSEE. Contact Benjamin Sprouse at [email protected].
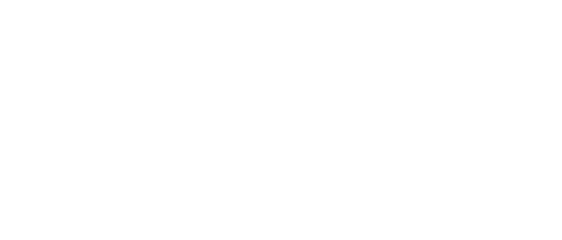
Leaders relevant to this article: