How zoned safety simplifies design and eliminates complicated safety circuits
An operator at a Midwest automotive assembly plant reaches through the safety light curtain of a machine that rivets two parts together. The machine automatically stops; he loads the first part into a nest; and the machine restarts after he is outside of the light curtain. While that portion of the machine is working, the operator steps through another light curtain and loads the second part into the machine’s riveter. After the rivet sequence is complete, the two components are joined and can be removed from the machine. It is then ready to start another cycle.
While it’s just another day on the job for the operator, the riveting machine is employing new technology that is revolutionizing machine safety (Figure 1).
Figure 1: The Medalist automated riveting machine uses the zoned safety concept to enable the operator to work in one zone while other zones in the machine continue to run.
(Source: Medalist Manufacturing)
It’s called the zoned safety concept. And it promises important benefits for machine builders, as well as equipment owners and operators. Zoned safety simplifies design, eliminates complicated safety circuits, improves machine productivity and reduces cost.
A better safety approach
At Medalist Manufacturing in Pella, Iowa, when we received an order to build an automated riveting machine, we’d been searching for a better way to meet today's operator safety requirements. The machine’s high cycling rate required the operator to move in and out of the part loading zones every 10 to 12 seconds.
Manufacturing companies must ensure the safety and health of their employees who are engaged in the installation, operation, adjustment and maintenance of production equipment. While the end user is responsible for training employees in safe work practices, the OEM must design and build a machine that is safe and compliant with government and industry regulations and directives.
As a manufacturer of custom industrial equipment for automotive, packaging and material-handling applications, Medalist pushes hard to embrace the highest standards and technologies. In this design, the company had to meet the Machinery Directive’s Category 3 architecture and a performance level of D (PLd). Category 3 requires redundancy or dual channels to achieve the required safety function: safe stopping of motion.
The conventional way to design safety functionality would be to dedicate one valve manifold to the safety circuit in the first loading station. Feeding that manifold would be an expensive redundant safety dump valve. A duplicate safety circuit would have to be installed in the second loading zone. But for a two-zone machine, this design would dump too much air, be cost-prohibitive and may not meet the higher cycle rates required, since most redundant dump-style valves are not designed to support higher-demand systems.
Medalist turned to the new zoned safety concept to achieve its safety functionality goals.
The zoned safety concept
As manufacturers focused on process improvement, the limitations of traditional safety systems on production-line productivity and cost became apparent. The objective was to develop lower-cost safety circuitry that could safely disable a section of a machine while the rest of the machine remained operational.
With this goal in mind, ASCO engineers pursued a simpler and less expensive approach to safety that would improve productivity while meeting the requirements of the Machinery Directive and ISO 13849-1.
The result was the Numatics 503 Series zoned safety manifold with G3 fieldbus electronics. This technology can control and reliably disable multiple and independent groups of pneumatic valves that operate a section of a machine. By using the 503 Series’ capability to integrate two safety zones within one manifold assembly, air and power are disabled only to the components required to enable the desired safety function: those that potentially might contact an operator and pose a risk. The rest of the machine can remain in operation when these safety circuits are enabled (Figure 2).
Figure 2: This manifold integrates a standard, non-safe pneumatic zone and two physically separate safety zones.
(Source: ASCO)
Green Section = Non-Safe/Standard; had no light curtain, low risk. This was used for vacuum tubes to remove rivet mandrels, as well as rivet gun trigger pilots. There were no hazards to protect.
Pink Zone = Safety Zone 1; had its own light curtain.
Blue Zone = Safety Zone 2; had its own light curtain.
Because zoned safety capability has been built on the Numatics 503 Series valve manifold platform, no redesign or safety redundant dump valve is required for zone control, and the user has optimal choices when selecting valve options, accessories and flow requirements.
The Numatics 503 Series zoned safety valve manifold provides multiple safety zones with the ability to have separate and redundant features for each of the safety circuits. It also allows for a non-safe section to coexist on the same zoned safety manifold, taking full advantage of the existing communications and I/O components. This pneumatic hardware provides machine designers the capability to create multiple zones or sections within a manifold that can be dedicated to safety functionality.
ALSO READ: The popularity of integrated control and safety continues to improve
Safely boost productivity
The zoned safety approach worked well for Medalist’s automated riveting machine. The application used two zones on the Numatics manifold —Safety Zone 1 and Safety Zone 2 — and a standard or non-safety section. Initially, this machine was designed with one safety zone. But Medalist realized that by adding a second zone, the operator could be working safely in one zone of the machine while the other zone was running. This substantially boosted the machine’s productivity.
Another important benefit was the ability to simplify the design of the safety circuit. A discrete safety circuit—with multiple redundant dump valves and other components that add complexity and higher cost—was no longer required to safely isolate different operator access points of the machine. The zoned safety approach improved throughput by not having to dump/exhaust the complete manifold and wait for it to recharge.
In addition, the zoned safety manifold allowed Medalist to meet the Machinery Directive’s Category 3 (redundancy) requirements, as well as achieve the required performance level.
No major technical challenges were encountered during installation. Numatics’ 3D CAD models were available online, simplifying design and configuration. Once the Ethernet mapping was completed, installation was straightforward and technical support was not required. Medalist engineers anticipated spending a day or two to configure this application for the first time. Within one hour, the safety circuits were up and running.
ASCO assisted Medalist in preparing the documentation that verified the machine’s ISO 13849-1 compliance. This work included providing Medalist with ASCO’s technical manual, which cited examples of adherence to ISO 13849 requirements, plus the CAD models of the zoned safety manifold.
The automated riveting machine has performed well in limited production runs for qualification and testing. While the new zoned safety technology is hidden to the operators, automotive plant management is aware of its benefits.
For both OEMs and equipment owners, zoned safety simplifies design and reduces cost while optimizing the safety of their machines. Best of all, productivity and asset availability are improved, since the user does not have to shut down the entire machine when safety circuits are enabled.
[sidebar id=4]
Russ Slaymaker is the head of controls and automation at Medalist Manufacturing, a provider of custom production equipment based in Pella, Iowa.
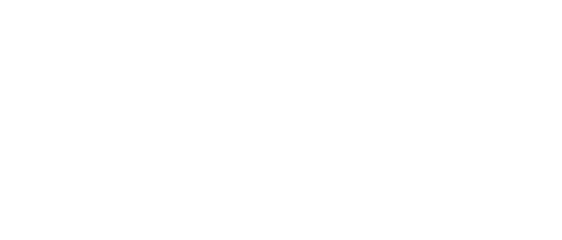
Leaders relevant to this article: