The wheels on cars and trains, turbines in power stations, the compressor in your refrigerator, all contain components that need to rotate with a minimum of friction, year after year, and often under heavy external pressure. The principle is a simple one: less friction, less energy. The bearings play a considerable role at each rotation in order to reduce friction and guarantee stable rotation. The requirements regarding the production process are respectively high, not least due to the final shape of the bearings and the finish during grinding and polish.
SEE ALSO: Wind Generators Prove Bigger Is Always Better
KMT, a builder of precision grinding machines, knows the critical importance of these machining issues well. The company is a merger of UVA International AB and KMT Lidköping, which were founded in 1928 and 1875, respectively. It has sales and aftermarket subsidiaries in the U.S., China and Germany. Production sites for new machines, rebuilds and repair work are in Sweden, and rebuilds also are done in Gurgaon, India.
Adjust to the Customer
KMT machines has been grinding components for the bearing industry during the past century, and during this time has continuously developed its technology to adapt to different customer applications. Today, wind power is a growing industry and an area KMT is focusing on.
"We follow our customers' development in new markets," says Thomas Karlsson, CEO of KMT. "When our customer was expanding in the area of wind power stations, new bearing types were needed. We were there with them, and developed new machines covering their needs."
Bearings are found in different locations in a wind power station turbine, such as on the fitting of the rotor blade, the turbine axes and the gearbox. The better that bearing performs its job, says Karlsson, the smoother is the turbine rotation and the lower the energy loss of the mechanic parts.
The rotating rotor blades are connected to the turbine axes through a bearing with a diameter of as much as 4 meters. Bearing rings of that size are ground by a Lidköping VTG4000 vertical grinding machine, through which the material gets its shape with the help of the optional combination of grinding and turning.
Critical Processing
Karlsson stresses how critical this process is, saying, "It is the grinding process that determines how accurate the recess (in which the ball will be placed) has to be. The accuracy determines the friction and, consequently, the accuracy of the power generation. But well-ground bearings with high precision offer, not only the possibility to reduce energy consumption, but also to improve their reliability."
If the rotor blades are positioned in the wrong axes under the stress of high wind forces, this might lead to severe consequences, Karlsson explains. The enormous power could loosen the blades and, in the worst case, the entire wind power station might collapse.
The reputation of Lidköping in the bearing machinery business has always been on high-speed and high-metal-removal rates. These capabilities are realized by the rigidity of Lidköping machine designs, with recognition that the stiffness inherent in each element of a machine's structure, when combined, contribute to its productivity overall.
Positioning and Quality
Positioning accuracy is very important, with a direct relationship to the quality of the finished bearings, Johansson states. Prior to the VTG4000, the company's largest machine could accommodate parts up to 600 mm (24 in.) in diameter, but the VTG400 handles diameters in excess of 4000 mm (157 in.), the size of the largest wind turbine bearings, while providing much greater accuracy.
Linear motors on the linear axes make the VTG4000 fast, and firm hydrostatic guide ways increase accuracy. With hydrostatic guide ways, pressurized oil injected between the top and bottom slides floats the top slide, creating a virtually friction-free and highly responsive slide system. "A standard size machine, using ballscrews on the axes, maintains about a 3-µm form deviation," Johannson explains. "This machine maintains form deviation of less than 1 µm with feed resolution in 0.1 µm steps."
Linear slides are at the heart of Lidköping machines, and the combination of hydrostatic guideways, air seals and linear motors creates a stiff, accurate, maintenance-free system. "To achieve dynamic stiffness we need high gain, which is linked to the quality of the encoder scales," Johansson adds. "It also makes a big difference that the angle encoders have the scale integrated directly onto the ring."
High Quality Improves Control of Turbine Blades
Pitch bearings allow wind turbine blades to optimize their angle according to wind speed, or create a stall condition in high winds, so the reliability of these bearings is critical to efficient, safe operation.
The multi-tasking VTG4000 is designed to machine these large bearings in a single set up, performing both turning and grinding with two separate heads. The two heads are configured as required, usually grinding/turning or grinding/grinding. The machine's 4.5 m X-axis carries the two heads on opposite sides of the part, and allows both grinding and turning tools to access the outside of the part. With some components weighing more than 35 tonnes, VTG4000 is very resistant to distortion and thermal variation, which is aided by closely controlled hydrostatic oil and coolant temperatures.
The grinding system/left ram employs a linear-motor-driven hydrostatic slide, has a vertical stroke of 860 mm, horizontal stroke of 2460 mm, and maximum acceleration of 1 m/s 2 with a maximum speed of 1 m/s. The resolution of 0. 01 mm is enabled through linear motors with servo-loop feedback from high-resolution encoders.
Source: KMT Lidköping
Johansson first saw the encoders that would end up on the VTG4000 at the EMO show in 2007, and Lidköping put the sensors through rigorous testing. "We compared different scales assembled on our reference slide, and selected the one with the best performance," Johansson says. "It was important that the linear encoders have a continuous length of at least 4.5 m, as well as high dirt resistance, and Renishaw's SiGNUM fit these requirements the best. We have fitted them to all four linear slides, and have had no problems. Our rotary table has the same design principle, with hydrostatic radial and axial bearings, air seals and torque motors. The rotary worktable's torque motor has a high-resolution encoder for the servo loop feedback. We did the same analysis and chose the SiGNUM angle encoders."
The encoders also help set the grinding spindle's angle, an important function of the machine. However, any out-of angle will be fine-tuned when dressing the grinding wheel, once again making use of the hydrostatic/linear motor slides' ultra-precision.
Renishaw's LM10 magnetic angle encoders are fitted to the B-axes of the grinding heads. These encoders are exposed to the harsh conditions of the machine environment, but their non-contact, non-optical design, and sealing to IP68, protects them from the effects of coolant and swarf. The digital or analog output LM10 allows up to 100 m travel and high-speed operation of up to 25 m/s (4 m/s at 1 µm resolution).
The encoders feature an integral set-up LED that speeds installation and removes the need for complex set-up equipment or oscilloscopes. "One of the best features of the Renishaw encoders is how easy they are to set up," Johansson adds. "With the scale attached and the readhead approximately located, the indicator lights make it very easy to see how well the two elements are aligned. Other brands could well have been used, however, we like the Renishaw product for its easy setup, precise resolution and high durability in tough environments."
To accurately set the part in the machine's work-coordinate system, the VTG4000 uses a Renishaw RMP60 radio signal transmission touch probe. After a raw part is placed on the bed, the RMP60 is loaded into the tool changer, and used to locate the exact position of key features in a matter of seconds. This data is used to update the coordinate system in-cycle for quick, accurate machining. The Renishaw touch probe is used for pre- and post-process measuring of the work piece. Pre-process shows exactly where and how the work piece is situated, as well as its stock allowance, out of roundness etc., and then post-process evaluates the result after hard turning and/or grinding.
Continue Reading
Latest from Encoders
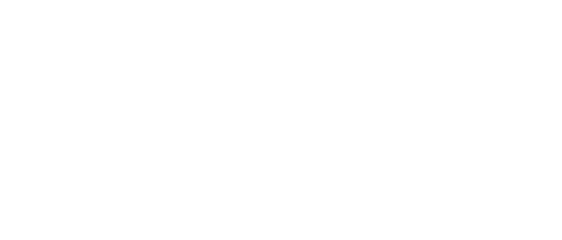
Leaders relevant to this article: