Servo systems lead the way to implement high-performance motion control
Servos have reigned for many years as the high-performance motion solution for applications such as robotics, machine control and material handling. Servo motor systems deliver precise, responsive and powerful control, but often at the expense of some implementation complexity. Following the “faster, better, cheaper” trend that started in aerospace a few decades ago, today’s servo drives are incorporating built-in features to improve ease of use and make servos work in more applications, while saving material and labor costs.
Servo systems
Servos are a type of electrical motor, usually with a rotating output shaft that can be connected to equipment directly or via a gearbox. As a dc motor, it provides high torque even when moving from zero speed. A key difference between a servo motor system, as compared to typical ac induction or dc motors, is that the servo motor incorporates an encoder used to provide positional feedback. Using this sensor, the servo motor operates as part of a closed-loop system and can thus be driven to particular rotational locations at dictated speeds, often following elaborate movement profiles (Figure 1).
While servo motor sizing and selection is important, the real brain behind the operation is a servo drive. The drive translates logical motion commands into an electrical signal driving the motor, and it interprets the feedback from the motor to ensure precise motion. Some servo drives can perform significant logical control internally, while others may be operated from a supervisory PLC, PC or other controller via a communication link such as Modbus TCP or EtherNet/IP.
Some typical servo system movements can be:
- rotating a filling machine turret at a fixed velocity
- accelerating and decelerating a conveyor to precisely space items on a belt
- moving X/Y/Z portions of a machine gantry from one position to another
- accelerating a robot joint from a standstill to a certain velocity and then decelerating back to a standstill so the joint stops where commanded.
While there are hard-coded approaches for performing these motions, many users would like a simplified approach for creating these moves and for implementing other advanced functionality.
Built-in control
Some of the newest servo drives take advantage of powerful processors and software to enable wizard-like functionality. Graphical user interfaces provide simple setup and programming, while support of standard communication protocols makes it straightforward to integrate servo drives with other systems. Following are a few built-in control features users can lean on to quickly create solutions for many types of common motion and application needs.
- Internal motion: While an external PLC or PC can certainly send commands to a drive, there are many smaller systems where it is better for the servo drive to provide native capability for users to configure logic and mathematical operations. In some cases, the drive can be an all-in-one logic and motion control solution.
- Electronic gearing: This is a feature where many secondary axes can be commanded at speeds that are a ratio of a primary axis. The ratios and even phase relationships can be changed instantly and on the fly so that machine elements move at the proper relational speed without needing gearboxes.
- Electronic camming: Physical cams operate mechanisms over a stroke and duration profile. Servos with electronic camming capability can reproduce these mechanical system movements, while adding the capability to be readily changed to match the needs of machine and product changeovers.
- Rotary and flying shears: These machines cut material on the fly and therefore require precise servo operation to move the cutter to match the material speed.
- Registration: Packaging, cutting and printing machines often take advantage of registration, which is using a detector to identify where moving product is located so a servo-driven portion of the machine can be driven exactly to where it is needed.
Figure 2: Servo drives can include built-in control functions, which can be configured using graphical user interfaces, providing OEMs and designers with the ability to create motion solutions quickly with minimal risk. (Source: AutomationDirect)
For each of these cases, users can create their own custom code in a servo drive or PLC. However, a modern servo drive that includes standard function blocks for these common functionalities simplifies and speeds designs, while providing a much higher level of standardization as compared to custom code (Figure 2).
This is especially the case when designers can drag and drop or otherwise select standard function blocks to carry out these elaborate tasks with proven reliability, eliminating the risk associated with more customized development.
Ready for startup
Servo motor systems are not simply turned on in the field, like a simple ac induction motor. Instead, they must be tuned and then function-tested in operation.
To meet user needs, servo drives should incorporate several tuning options:
- static auto tuning
- running auto tuning
- assisted tuning
- manual tuning
Auto tuning is the most popular option because it offers a simplified approach that works in most cases. A user can trigger one-touch auto tuning to evaluate the motor while it is stopped or a normal auto tuning to provide better information by evaluating the motor as it makes point-to-point moves. More advanced users may opt for assisted tuning where they adjust the desired responsiveness while the drive analyzes the moving system, or they can perform manual tuning to adjust more than a dozen parameters and fine tune the system.
Once installed and tuned, it is time to run the equipment and verify proper functionality. Servo motion systems can be very fast-acting and by nature demand precise in operation. Sometimes it can be difficult to observe each event accurately or troubleshoot a problem.
Figure 3: Some servo drives incorporate advanced capabilities, such as a built-in oscilloscope, to help users quickly commission and fine-tune operation or troubleshoot if the need arises. (Source: AutomationDirect)
In the past, this often meant a technician needed to use test meters, an oscilloscope and perhaps even a high-frame-rate video camera to investigate. However, servo drives have much improved processing power and can incorporate an on-board oscilloscope—built-in to the setup software—for monitoring as many as eight channels (Figure 3).
This provides a convenient way for users to review operation, zoom in on areas of interest and overlay multiple traces. With these capabilities, users can compare commanded to actual positions and then adjust various operating parameters to improve motion response.
Also read: SureServo2
More applications implemented more easily
Servo drive and motor systems are a key technology used by end users and OEMs for many types of equipment motion control applications. They provide the necessary top-grade performance but can be complex to configure and commission.
By providing advanced processing and flexible configurability with many standard functions and setup/diagnostic tools such as auto tuning and oscilloscopes, modern servo systems give users of all types easier and less risky options for applying servo control in a wide variety of applications.
About the author
Chip McDaniel works in technical marketing for AutomationDirect and is a graduate of Georgia Tech. His decades of experience in the industrial automation field include designing, building and commissioning multi-axis servo systems. Contact him at [email protected].
Sponsored Recommendations
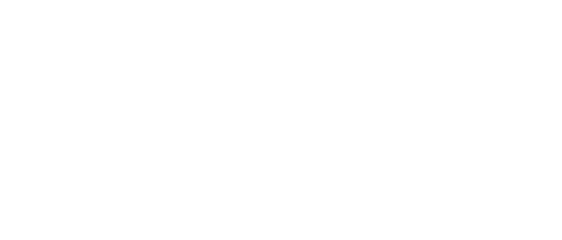
Leaders relevant to this article: