Data-driven smart system improves printing production
The rapid introduction of Industry 4.0 (i4.0) technologies is transforming manufacturing across a broad range of industries, including packaging printing. Data-driven smart systems offer major advances in manufacturing speed and agility for increased productivity and less downtime and waste. All are part of the requirements for a flexible factory-of-the-future production environment.
Many companies are actively exploring and integrating i4.0 technologies in order to make the Factory of the Future a reality today. This includes Barry-Wehmiller’s Paper Converting Machine Company (PCMC) in Green Bay, Wisconsin, a supplier of equipment for flexographic printing, bag and tissue converting, packaging, and nonwovens technology. Using advanced intelligence and machine-learning capabilities in the drives and controls platform provided by Bosch Rexroth, PCMC recently introduced an award-winning i4.0 smart technology solution called SteadyPrint that solves the longstanding problem of bounce in flexographic printing. SteadyPrint is just one element in PCMC’s suite of SmartLink i4.0 technology, which consists of smart features for connected machines.
Applied technology to solve bounce
Printing is centuries old, with modern printing concepts invented by Gutenberg in the 15th century. Since then, printing has been as much an art as a science, even with the advent of high-speed flexographic printing systems, a form of rotary printing where ink is applied to a variety of surfaces using flexible rubber or similar printing plates. Although these systems incorporate advanced automation that enables printing complex jobs at speeds up to 2,000 feet per minute, certain aspects of printing operations often depend on an operator’s artful manipulation—tweaking—of the press at startup in order to print a perfect image.
Waste associated with the issue of bounce is most often seen at the start of print runs with challenging graphics. These challenging graphics often have a hard leading edge on a printing plate that meets the opposing impression roll, causing an impact that affects print registration. This leads to poor print quality, with uneven ink distribution or colors that are out of registration. Press operators typically tweak various settings on the press manually until they minimize out the bounce effect, at times being unable to fully eliminate these negative effects on the print quality.
Every flexographic printer struggles with certain bounce jobs. In printing, the overall goal is to get the presses quickly up and running at full speed, keeping the amount of setup time and wasted material as low as possible. Bounce leads to wasted time and materials, and companies must depend on experienced press operators to fine-tune print settings and still get the press running at the highest possible machine speed with quality output.
To eliminate the tweaking, PCMC incorporated i4.0 technology in its new SteadyPrint feature. This solution reduces print setup time, increases quality and reduces print waste, even with less-experienced machine operators. Working under a long-established relationship, PCMC tapped into Bosch Rexroth for a unique array of resources and capabilities to help develop SteadyPrint, including:
- decades-long expertise and innovation in printing and converting technologies
- intelligent motion control technology that can learn and respond with torque offsets
- support for high-speed SERCOS communications architecture for real-time motion control advantages
- Rexroth’s Open Core Interface tool that enables access to additional motion control functionality and analysis using third-party programming languages.
SteadyPrint solution delivers results
PCMC worked with Bosch Rexroth and distributor partner CMA/Flodyne/Hydradyne in De Pere, Wisconsin, to develop the SteadyPrint functionality for the company’s Fusion and ELSMax flexographic printing presses (Figure 1).
Figure 1: The Fusion flexographic press from Barry-Wehmiller’s PCMC features data-driven smart systems that offer major advances in manufacturing speed and agility for increased productivity and less downtime and waste.
(Source: PCMC)
SteadyPrint is based on a disturbance-canceling algorithm that uses the intelligence in the Rexroth servo drives to learn the electronic signature of each print job and rapidly cancel out the disturbance that generates bounce. When customers were given the opportunity to test the feature by bringing sample jobs into PCMC, they were able to improve press speeds between 200% and 400% and reduce waste by up to 35%.
We had multiple customers come in to do bounce trials and, while every customer’s print job is different, all of them doubled or tripled the speed or went to full speed much faster than ever before. One customer had a complex job that could only run at 300 feet per minute on the press due to bounce. It ran the same job on our Fusion press with SteadyPrint at 1,500 feet per minute with no operator adjustment (Figure 2).
Figure 2: Before, the bounce in a complex job slowed the printing, but the Fusion press with SteadyPrint ran five times faster with no operator adjustment required.
(Source: PCMC)
How SteadyPrint stabilization works
Each Fusion press system consists of a large central impression cylinder, 8 to 10 feet in diameter, surrounded by eight or 10 printing decks with two cylinders, one containing the image and the other applying the ink.
The Fusion press, like other PCMC presses, was already using Bosch Rexroth drive and control technology, including IndraDrive M servo drives (Figure 3) and IndraDyn T frameless torque motors to control the cylinders, and the IndraMotion MLC motion logic automation platform for overall machine control.
Figure 3: The capabilities of the servo drives enables the SteadyPrint feature to gather axis motion data and use in a drive-based algorithm to smooth out print quality and eliminate bounce.
(Source: PCMC)
To develop SteadyPrint, the capabilities inherent in the Rexroth IndraDrive servo drives were utilized to gather new data about the motion on each axis. “Our IndraDrive servo drive registers bounce as a torque disturbance,” says Brian Schmidt a motion control engineer at Rexroth. “The drive will counteract the disturbance and smooth out the motion, but, while the disturbance is happening, print quality is adversely affected. By capturing data on the torque feedback, velocity feedback and position feedback of the drives, the torque feedback had a signature that repeated once per rotation of the roll.”
We developed a concept to record this pattern, continues Schmidt. “We then apply a compensation algorithm, to offset the effects of the torque disturbance significantly reducing position errors,” he says.
According to Schmidt, for each print job, it takes just a few rotations of the cylinders for the drives to learn the necessary torque offset to apply; the SteadyPrint feature then engages the drive-based algorithm and virtually eliminates the need for operators to make manual mechanical adjustments to smooth out print quality and eliminate bounce. This also eliminates the wasted material from mechanical adjustment and enables full-speed printing almost from the outset of each print run.
Adding refinements to the Fusion press mechanical design to minimize deflection, including an improved mandrel support arrangement that increases deck stability, PCMC is using the IndraDrive drive-based torque offset algorithm to implement its SteadyPrint capability across the full line of Fusion press systems, as well as the company’s ELSMax presses.
Intelligent drives deliver major advantages
The SteadyPrint feature confirms a core advantage of Bosch Rexroth’s approach to automation and motion control: Using distributed, drive-integrated intelligence to solve motion control challenges is often the smartest and most effective approach, rather than depending on a PLC to handle all the processing.
There is no way we could do this if the intelligence wasn’t in the drive. Given the speed and dynamics of how these print jobs run 1,000 to 2,000 feet per minute, with repeats as low as 12 inches long, it wouldn’t be possible to have the controller handle the compensation. It has to be in the drive.
Bosch Rexroth’s use of the high-speed SERCOS Ethernet-based communications bus as the backbone for its motion control platform has also enabled PCMC to advance its connected machine concept. With SERCOS, we have an expanded view of all the data that the drive captures. “That lets us have a deeper look into the drive and allows us to implement system dashboards and predictive maintenance capabilities where we can connect remotely through the cloud to support customers in real time to manage their systems,” says Schmidt.
Bosch Rexroth’s Open Core Interface enhances PCMC’s flexibility to provide connected machine functionality to its customers. The Open Core Interface is a machine control programming interface to create high-level, language-based applications. PCMC utilized Open Core Interface to extract data from the drives, such as torque, position and velocity data and then made it available for analysis using third-party programming languages and data analytics packages, rather than going through traditional PLC methods of exchanging data.
Collaboration wins awards
The Flexographic Technical Association (FTA) recently awarded its Technical Innovation Award, Heavy Metal Category, to PCMC for the SteadyPrint system. I credit the close working partnership our people developed through multiple innovation sessions and system refinements for the success and recognition that SteadyPrint has accomplished.
The best compliment I can pay is that the project went as expected. I have a very high view of what Rexroth and CMA/Flodyne/Hydradyne bring to these kinds of projects, and their capabilities are always impressive to the highest degree. I couldn’t have imagined doing it with any other team. They are the gold standard in product and support. I also appreciate how our partners are committed to real-world applications of Industry 4.0 technology and how they are helping PCMC to implement and expand the SmartLink concept of smart features and connected machines. PCMC plans to continue introducing new innovations like SteadyPrint and looks forward to working with Bosch Rexroth and CMA and to produce the next generation of innovations.
Rodney Pennings is the Printing, Coating and Laminating sales director at Paper Converting Machine Company (PCMC, a division of Barry-Wehmiller and a leading supplier of high-performance converting machinery for the tissue, nonwovens and package-printing industries worldwide. He joined PCMC more than 21 years ago and also helps to direct the product line’s strategy and market plans.
ALSO READ: How to streamline machine control
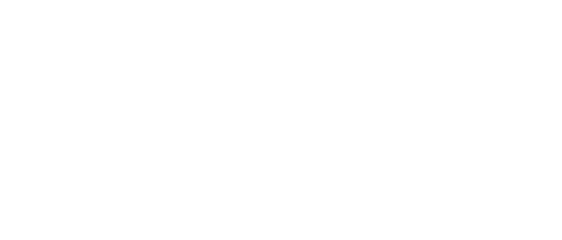
Leaders relevant to this article: