Over the years, we have reinvented and repurposed JLS Automation as necessary and moved into new markets as we identified trends and opportunities. More than a decade ago, we decided to focus on hygienic packaging solutions for the food industry, including primary and secondary packaging systems. Although we had some food customers, it was an uphill battle because we simply had no brand identity.
As we moved into meat, poultry, dairy, and frozen foods, we discovered these spaces were very skeptical of technology and had almost impossible-to-meet ROI targets. It made selling equipment in these harsh sanitary environments difficult. We tried to focus on applications where we could design it once and build it many times, but it was still a challenge to meet the financial constraints in these markets.
Despite the challenges, we decided to focus on the technology of vision-guided robotics and apply it to high-sanitary machinery. Even today, it is not a highly served space in terms of suppliers. It’s a rapidly growing niche, and we worked hard to establish ourselves in this space as a recognized leader.
Most food companies had not heard of us, and it made for some tough sledding. We also had to compete with some large European equipment suppliers that were in the same space and had a strong following. It was difficult getting a foothold.
Located in York, Pennsylvania, JLS Automation was founded by Joseph L. Souser (JLS) in 1955 as a manufacturer’s-rep firm, and there have been many big changes since then. There is a lot to that story. Some changes were very deliberate, and some were forced by marketplace conditions, markets we served and customers coming and going. Today, and in the future, technology is making us successful.
High-sanitary technology
Figure 1: The Osprey Robotic Case Packer is space-efficient and designed to integrate with existing packaging systems packing multiple products and packaging styles with quick changeover.
(source: JLS Automation)
Virtually 100% of our machines use vision-guided robotics, which is becoming a big thing in high-sanitary machinery (Figure 1). The two elements that put us in somewhat of a unique position is vision guidance plus high-sanitary capabilities. There are folks that make sanitary equipment, but not vision-guided, and there is vision-guided equipment, but not sanitary.
We developed a machine called the Osprey case packer specifically aimed to be adjacent to washdown areas. It's a case packer, but designed to meet environmental requirements and motion requirements based on the somewhat random presentation of a package. It was designed and optimized to be downstream of thermoforming machines but is suited to handle a variety of other products/packages.
With the vision guidance, the machine can handle products and packages that are not soldered neatly. Products are often slammed onto a conveyor at the output of the thermoformer machine and shoved onto a conveyor where we have to meter them and spread them out on a belt and then pick them, regardless of their orientation, and place them in a case. It's a good application for vision-guided robotics technology.
The use of vision-guided robotics also makes it easy to change the end effector and then pick and case-pack a completely different product, such as a ground beef, sausage or cookie dough chub. Different configurations enable it to function as a tray loader.
Simply standardize
Figure 2: There's no need to stop the box to load it as vision guidance, encoder tracking and a photo eye provide the needed control signals to pack on the fly.
(source: JLS Automation)
Approximately 80-90% of the machine elements are the same, whether the machine is downstream of a thermoformer, chub maker or tray line. It uses standard solutions that can be built quickly and built to stock instead of starting from a clean sheet of paper.
Control cabinets are examples where standardization helps. Even in our large, highly engineered systems, we are still trying to standardize. Even so, our off-the-shelf machines have cost and lead-time constraints that our more custom machines may not. By standardizing on Hoffman enclosures and cabinets, we have a partner that can meet our quality and delivery needs, regardless of the project.
Hoffman is able to meet the demand for high-quality stainless steel solutions in the form of Watershed and Concept enclosures. The ability to customize enclosures to meet unique size and cutout requirements was also a great advantage. They help us from a supply-chain standpoint, manage inventory and lower cost to keep the equipment available and respond to the market without us having to stock cabinets or make design changes.
We work hard to standardize our designs. For example, although we don't always need them, we use a common build, standard design that integrates motors in the conveyor rollers. The pinch belts that position the cases as they are loaded, regardless of the packages we are going to pick and place, are another common design (Figure 2).
The integrated motor conveyor rollers and round machine frames help with sanitary requirements. The cabinets we buy from Hoffman are sloped top. With sanitation, the devil is in the details. When you open the cabinet, there is a slope on the lip, not a flat surface. Flat, horizontal surfaces are the enemy, and anywhere we can eliminate them we do.
Vision guidance and better handling
Many case-packing machines will stop a case or cases in a static location and place packages into one or several cases at one time. With the addition of vision guidance and tracking, the cases don't need to stop. They move slowly through the system on a pinch belt conveyor and are tracked with an encoder and a sensor to detect the leading edge of the box.
The robot uses vision guidance to find the product and adaptively pick it up before packing the case. Changeover is easy as there is no flight conveyor spacing to worry about. There are simply fewer parts and very few changeover parts, typically just the robot end effector, which saves time and money.
The robotics can also be gentler when handling a product. For example, a bakery often makes product that is fragile. With a traditional gantry-style, “bang-bang” case packer, it pattern-forms the packages to build a layer and then loads that into the case using pneumatics and moving products to hard stops. That can and does damage the contents. Using the robot, it is easy to control how aggressively the product is picked, moved and placed.
Fewer control cabinets but better control
Figure 3: The new controls platform combines the robot, motion, logic and HMI into one controller, eliminating many parts yet providing more powerful control.
(source: JLS Automation)
We have a lot less equipment and fewer control cabinets, due to our new control system design. Historically, we used ABB robots with Rockwell Automation PLCs, HMIs and variable frequency drives. That has been successful over the years. With our new machines, ABB didn't have everything we needed nor the payload required.With our new generation of machine offerings, we are using Codian Robots and a B&R Automation controls platform that integrates the motion, logic and HMI into one controller (Figure 3). It uses one hardware space and one software space. This configuration has eliminated a huge number of parts including electrical and software interfaces. The result is a more powerful but less complicated control system.
Codian Robotics focuses on providing delta pick-and-place robots. They don’t do controls, and they don’t build SCARA or six-axis robot arms. They make deltas. They also have a hygienic line. Customers don't like the idea of painted robots or carbon fiber above food products. Codian robots are all stainless with the lower arms titanium-jacketed. It's a much more food-safe, food-friendly robot. A B&R control platform runs it.
Rockwell Automation and B&R have similar capabilities. They both offer logic controllers, HMIs, servo controllers and VFDs, but B&R works well for use from a price, value and performance perspective. With our new generation of controls, we expected customers to accept the change from ABB to Codian with B&R Automation controlling it, but they would still want Rockwell as the PLC and HMI solution. That hasn't been the case as our customers understand the value of this solution. The B&R hardware is controlling everything.
Less is more control
For new designs at JLS Automation, we use both Power Panel or Automation PCs from B&R Industrial Automation. It's PLC, motion and visualization all in one device. The B&R solution is a controller you can hold in your hand. It's about 3-by-5 inches and an inch-and-a-half deep that plugs on the back of a touchscreen display and contains the code for the robot motion, PLC control and HMI graphics. It's all together in the same software platform. We also integrate B&R safety technology.
B&R’s motion is outstanding, and the safety and HMI capabilities are other reasons they have been so successful, in non-motion-intensive applications.
The controllers we use talk to distributed I/O using Powerlink. It's B&R's go-to Industrial Ethernet solution, and it is very fast and deterministic. I think it competes well with EtherCAT, EtherNet/IP and Profinet.
We use maybe 16 inputs and 16 outputs, and the rest is Industrial Ethernet or fieldbus or it's tightly integrated. There just isn't as much I/O needed. Most of our I/O is safety-related or a few sensors and interfaces to an upstream or downstream machine. The fewer the number of terminations, the better.
The robot is controlled by the B&R controller and includes B&R servo amps and servo motors. The entire control platform is B&R. However, some electrical devices, such as pilot lights, push buttons, circuit breakers and disconnects, are all Rockwell Automation. It keeps Rockwell products on our machines which is important to many of our customers as they keep some of these common elements in their stores.
In the past, we used ABB's PickMaster 3 software product as part of our robot integration for picking and packing integration along with its advanced vision and conveyor tracking capability. Some years ago, we switched over to Cognex In-Sight vision systems and continue to use it today with each camera providing guidance information on up to two robots.
The In-Sight has all the tools that we need, but it is one more thing to integrate.
However, at the end of last year, B&R announced it will offer an integrated vision solution. We'll watch and see how well control, motion, HMI and vision integrate into a single controller. It's another level of tighter integration; do it all with just one controller.
Windows not required
Once we show the customer what we accomplished with our B&R control system, physically and in the software, it's usually an “aha moment” for the customer.
One of the things that swayed our opinion was that B&R does not run Windows. Physically, it runs an Intel chipset and is technically a PC that can run Windows, but you don't have to. They have their own operating system, and we felt that is a big advantage. Many of our historical problems with some of the previous platforms that required a PC to do the motion and vision were the headaches that were PC- and Windows-related, not robot-related. We have worked hard-to-keep Windows out of our equipment, and B&R allowed us to do that.
The technology in the PC-based design provides servo update times that are incredibly fast; scan rates are off the charts; and they have good value. Their price points are lower and they are physically smaller, as well.
More control in software
We have very strong knowledge of tracking conveyors and encoder information and passing high-speed, important data around efficiently and quickly and adapting that information with vision inspection results. It is our expertise and what we do.
We use B&R Automation Studio 4 for program development, and its built-in libraries help speed programming. We use function-block programming, but we create many of our own control algorithms and function blocks.
Probably the most significant algorithm we created started with some of B&R robotic kinematics motion-path planning. After working with it, the software platform allowed us to create our own custom functions. The canned approach worked, but the system openness allowed us to create an improved machine specific solution. We had a better way to do it that was better for us in the long run.
Although painful to develop, we now own it, and it makes our equipment special. It does what we need it to do without any overhead. There was some pretty intense math by our developers. When he first told me what he was going to do, I told him he was crazy. That's for robot companies, not for us, but he did it and it works great. Our new solution involves almost no actual motion programming; everything is done on the HMI via a series of configuration tools saving significant engineering effort. We are planning on our service department handling some of the simpler applications on the floor, in many cases eliminating the need for engineering to have to set up the recipes.
We had also taken a very big step over the last few years, starting with ABB and PickMaster, but we had all these Windows issues and found it to be a very constrained environment. It was made to do some things very easily, but if you needed do significant customization; you were stuck.
We ended up developing EyeQ Tracker, which is our own conveyor tracking algorithm and approach. With that, we took PickMaster and all associated overhead costs and physical costs, the PC in particular, and got rid of it. It simplified our machines, even before we switched to B&R controls hardware. That has evolved over the years, and we took those algorithms, written in ABB's language, and rewrote them in B&R's programming environment. We have EyeQ Tracker solutions for both ABB and B&R.
ALSO READ: Accurate fishing begins with lights-out manufacturing
Better and much less integration
Figure 4: The capabilities of the control system eliminated control enclosures, and the remaining one reduced cost, size, number of components and wiring complexity.
(source: JLS Automation)
On our dual head Osprey machine, we used to install our control panels on top of the machine because they were so large. With the B&R platform, those cabinets are gone. Everything is in the cabinet that is on the machine. We have seen significant interest in the economy of scale in our smaller control enclosure (Figure 4).
We also like to show off our wiring, because there is not a lot of it. It's a very simple control system, physically. The previous wiring went to racks of I/O, encoder termination boards, drives, a PLC, robot controllers and an HMI. The integration of the B&R hardware has greatly reduced that. We reduced the cost, size, number of components and wiring complexity while increasing the control capability.
It is also more reliable. There used to be many connections between the PLC and robot controller, and, if a connection comes loose, a technician needs to troubleshoot the problem. We don't have that connection anymore; it's all one controller and the same program. We just have fewer things to fail, which by definition is more success.
The feedback with this next-generation control system has been great. A customer called early this year and said, "Look, I had to call you because I had no idea where my maintenance information is. I never used it and wanted to do some preventive maintenance on the machine, but we never touched it other than to start and stop it. It just runs." We enjoy hearing those comments, and the mechanical design, control system and programming is how we got there.
Leveraging standard designs, reducing control hardware cost and complexity and a tightly integrated control system has led to our success. We are moving into a new facility, with twice the square footage, by doing the right things. The market is ready for technology to help keep the equipment running.
Sponsored Recommendations
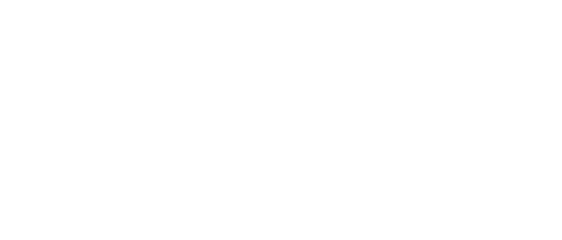
Leaders relevant to this article: