Figure 1: Hilmot MDR accumulating spiral is bidirectional and capable of variable speed control.
(Source: Hilmot)
Hilmot is a conveyor manufacturer with a focus on 24 Vdc motorized drive roller conveyors. Located in Milwaukee, Wisconsin, Hilmot also offers product sortation and tire handling systems along with traditional products, such as belt conveyors and belt-driven live roller systems (Figure 1). It also provides extendable conveyors, scanners, weight scales and related products for a complete solution. It provides design options and the ability to expand in the future.
Hilmot is working to redefine the conveyor in the material-handling industry with energy-efficient design, reduction of system footprint, low noise and simple maintenance. Its big claim to fame is the motorized drive roller (MDR).
Efficient and simple conveyors
MDRs are the next generation of powered roller conveyor systems, and industry should take note. Traditional conveyor systems use large, inefficient motors that run continuously and power up long stretches of conveyor. MDRs turn on only as needed, transporting products through smaller zones. Hilmot's systems give its customers the functionality and efficiency they need and reduce maintenance time. The simplicity, interchangeability and serviceability of our product line and AS-Interface are key benefits our customers value.
Hilmot is constantly working to improve its innovative technologies in material-handling applications. Hilmot turned to Pepperl+Fuchs, which leveraged the advantages of AS-Interface and developed a motor-control module compatible with Hilmot's MDR applications.
Hilmot’s H-20 line of MDR systems brings a new dimension to control, programming and visibility of conveyor systems. AS-Interface open architecture allows additional devices and safety products to be added to the system seamlessly. Programmers gain access to valuable device status and MDR diagnostics and have complete visibility and control of the system from a centralized location.
Hilmot's MDR design is an on-demand system, instead of always-on. The MDR conveyors use a series of sensors and logic to sense and control where totes, bins and tires are and only move them when necessary. This reduces the energy use and increases the service lifetime of the conveyor system.
Heavier loads are possible with MDR. There are many conveyor applications where the MDR is replacing the chain and sprocket and the belt such as in spiral conveyors, gates, lifts and pop ups. Instead of taking hours to repair a conveyor or belt, MDR is replaced in minutes due to its simplicity and reduced components. Pop out the problem roller, insert a new one and reconnect the wire.
AS-Interface to conveyors
Actuator-sensor interface (AS-Interface) is an open industrial networking solution that reduces wiring complexity and increases control functionality, making it an excellent solution for MDR conveyer systems. Pepperl+Fuchs' AS-Interface motor-control module H-20 has allowed Hilmot to provide customers with advanced functionality and safety. It is equipped with two sensor inputs, two motor control outputs and two motor power connections, providing control for up to two individually powered conveyor zones. The module provides up to 5 A starting current for each motor. Controls engineers now have the ability to easily program:
- eight speed settings for the motorized drive rollers in each zone
- eight acceleration/deceleration profiles for soft starting/soft stopping motorized drive rollers
- direction of the motorized drive rollers for each zone.
Configuring speed or ramp profiles of motorized drive rollers is most easily done using add-on instructions or function blocks. An H-20 add-on instruction is available for Rockwell Automation PLCs, and H-20 function blocks are also available for Siemens PLCs to set the desired configuration. These instructions enable changes to be made to various parameters while the conveyors are running. When other PLCs are desired for application, changes to speed settings and acceleration/deceleration profiles must be done using commands outlined in the AS-Interface Command Interface manual.
Control Details
Figure 2: Hilmot’s MDR conveyor has a modular design that allows for infinite layout options.
(Source: Hilmot)
The H-20 motor-control card is configured with an ASI handheld programmer to give it a node address for the PLC to reference. The connection to the H-20 is through a flat black cable which provides 24-Vdc, 15-A power and is connected using insulation displacement technology. A separate yellow flat cable provides communication using the same connection method. Up to 62 H-20 modules can be connected on an AS-Interface network with up to 124 H-20 modules using an AS-Interface gateway.
The 24 Vdc provides drive power to the roller, belts and lifting motion eliminating the need for pneumatic solenoids and tubing (Figure 2). This all-electric design is quiet, consistent and easy to maintain, and zero pressure accumulation is standard.
Each H-20 module is assigned a node address. Ultimately, all the nodes get mapped into an AS-Interface master, which are directly accessible from a PLC for control. H-20 motor-control modules are controlled via digital output bits mapped from the PLC. Each H-20 module is set up to control two motorized drive rollers or two conveyor zones consisting of multiple rollers. Each motorized drive roller is connected to an output on the module. A PLC starts and stops the motors using two bits. Direction of the rollers in the zone can be controlled using a PLC bit, as well.
Safety
Additionally, if machine safety is a priority, Cat. 4, SIL 3, safety levels are easily achieved with AS-Interface. AS-Interface Safety at Work makes it possible to implement a safety-control system compliant with ISO 13849-1 up to PL e, or up to SIL 3, according to IEC 62061. While the use of AS-Interface Safety at Work itself does not guarantee that the resulting system will be safety-compliant, AS-Interface Safety at Work can provide the necessary architecture, component reliability and redundancy to create a safety-compliant system.
As with any safety-system implementation, the designer should first perform a complete risk assessment to identify specific machinery hazards, attempt to mitigate as many as possible through thoughtful mechanical designs or fixed safeguards and then address remaining hazards with carefully selected safety devices and safety controls.
Components and systems designed to meet PL e or SIL 3 would be required in any application where there is any risk of severe or irreversible injury during any human interaction with the machinery. Obvious areas might include load/unload stations, manual sorting or inspection zones. However, less obvious applications would involve any piece of equipment that might require human intervention at any time during its lifecycle, including routine maintenance or breakdown repair tasks.
ALSO READ: Consider machine integration in the design phase
Innovative focus
Figure 3: With a mounting depth of just 27 mm, the motor control module is mounted directly into conveyor frames, which hides the wiring completely.
(Source: Hilmot)
The fully integrated AS-Interface module for dc MDRs was specifically designed to help meet the speed, cost and energy constraints of the most demanding material-handling applications. In addition to reducing the work required to wire motor starters, the module also ensures reliable motor operation through its tailor-made functions, boosting build speed and operating efficiency of MDR designs for both Hilmot and its customers.
With a mounting depth of just 27 mm, the motor control module is mounted directly into conveyor frames, which hides the wiring completely (Figure 3). Mounting inside the frame is easy and can be done without tools. The module is enclosed by a durable, shock-resistant, IP67-rated plastic housing with a one-piece design, eliminating device assembly. Sensors and MDRs are connected using integrated motor and sensor cordsets that dramatically improve installation speed while reducing costs and overall complexity. The universal control platform made possible by AS-Interface allows Hilmot to reduce the number of communication protocols in its product line.
Once the module has been attached to the conveyor frame, inserting the AS-Interface and AUX flat cables is the final step of the mounting procedure. This dramatically reduces the time needed by Hilmot’s installation team to set up systems at customers’ facilities. Using AS-Interface, entire conveyor systems, including all other control components, can be split into manageable segments—ready to be transported, installed and extended independently from one another.
MDR systems are now equipped with Pepperl+Fuchs AS-Interface, resulting in an innovative solution that marks a major advance for conveyor technology. Pepperl+Fuchs offers a broad portfolio of AS-Interface products. AS-Interface replaces conventional wiring technology in a wide range of applications, dramatically minimizing installation costs and opening up new control, diagnostic and safety functionality.
Jeff Berken is vice president of sales, marketing & customer service at Hilmot. Berken has been in the material-handling business for more than 16 years and has worked out of Hilmot’s corporate headquarters in Milwaukee, Wisconsin for 11 years. Contact him at [email protected].
Sponsored Recommendations
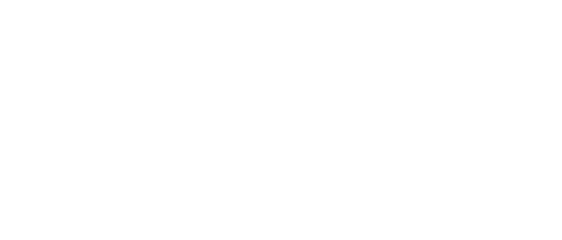
Leaders relevant to this article: