Pressure transmitters are widely applied for a variety of measurement purposes, and they cause a lot of trouble. Zeros shift, lines plug, and readings become erratic. But fundamentally, there's no reason to have pressure measurement problems. All over the world there are transmitter installations giving consistent, accurate pressure readings in the most difficult applications. The key is to specify and install pressure transmitters wisely.
The heart (and in many cases, the limitation) of a pressure transmitter is the transducer (an overview is in the sidebar, Transducer Technologies). The critical factors used to select a transducer are its accuracy, the system pressure and temperature, and fluid characteristics.
A pressure transmitter consists of several components including the sensor, signal-processing electronics, and signal-conditioning electronics. The sensor translates force from pressure acting on an area into an electrical signal--usually a millivoltage or voltage--that is amplified and converted by signal-processing circuitry The conditioning electronics convert the sensor output to a standard signal such as 4-20 mA, 0-10 VDC, etc.
The strain-gauge pressure transducer converts pressure (a force) to a resistance change proportional to the applied strain. The strain gauge circuit consists of one, two, or four variable-precision resistors in a Wheatstone-bridge configuration. When the resistors are subjected to pressure they deform, changing the resistance of the circuit. A strain gauge sends a millivolt output signal.
Some advantages of the strain-gauge sensor are that it is widely available from many vendors and has good immunity to shock and vibration. Principle limitations include sensitivity to swings in temperature (more sophisticated designs have temperature compensation) and limited temperature and pressure ranges.
The output of a capacitive sensor is proportional to the change in capacitance of two diaphragms (plates) inside the transducer. Applied pressure changes the distance between the two plates, causing a change in the capacitance that is detected by an oscillator circuit. Analog transmitters convert the frequency to a voltage, while digital transmitters work directly from the sampled frequency.
The principal limitation of capacitive sensors is that they are somewhat sensitive to vibration. They provide excellent response and stability, and are widely applied in many pressure transmitter manufacturers' designs. This large installed base allows the instrument engineer to draw on a great deal of installation experience when choosing this type of transducer.
In a quartz resonator sensor, pressure results in a change in frequency across the resonator that is directly proportional to the applied force. These transducers can be scaled over a wide range of pressures, and typically contain a quartz-crystal temperature sensor for temperature compensation. This type of sensor can offer increased immunity to temperature, vibration, and acceleration.
The vibrating wire and cylinder sensor has a wire excited by a magnetic coil. The wire vibrates at its resonant frequency in a phased locked loop (PLL) electrical circuit. A pressure-sensing diaphragm changes the tension in the vibrating wire, causing a change in resonant frequency proportional to the applied pressure.
Examine Accuracy
Controls experts such as Bala Liptok have said inaccuracy is probably a better measure of instrument performance. Engineers must recognize that many accuracy statements may be formulated based on laboratory-like conditions that are much more benign than the dirty and electrically noisy environment seen by a pressure transmitter inside a plant.
The engineer should ask the transmitter manufacturer two questions:
1. Is every transmitter tested to meet the accuracy specification?
2. If only a representative sample of transmitters is tested, what statistical method was used to develop the statement? Statistical criteria include the size of the population, statistical limits of error, and confidence.
Ask about effects of factors such as humidity and vibration on hysteresis, linearity, drift, and repeatability (Table I). Each pressure transmitter has an accuracy envelope determined by base accuracy, ambient and process exposure, and drift.
It is common for manufacturers to combine linearity, hysteresis, and repeatability into the base or nominal accuracy. The primary contributors to error are temperature and, in the case of differential pressure measurements, static pressure.
Determine Pressure and Temperature Ranges
Examine the pressure application and determine the maximum pressure that the transmitter will see.
Consider the following values:
1. The normal operating pressure range, low and high.
2. The maximum abnormal operating pressure range, low and high.
3. The maximum safe overpressure range (burst or damage limits).
4. Peak and frequency of pressure pulses.
The low limit of pressure must be considered if the transmitter can be damaged by vacuum and could be exposed to vacuum. Users should also pay attention to the hydrotest pressure associated with the line, though this does not tend to be a problem. Also, if the sensor is directly exposed to high temperature, the pressure rating will be limited by that temperature. Exposure to abnormal events (such as water hammer) must also be taken into account.
Once the pressure limits are determined, it is good practice to allow a 20% safety factor. If there is an overpressure or safety device, the pressure rating of the transmitter can be at the trip setting of the overpressure device.
Over-rating a transmitter can negatively impact its range and sensitivity. These two parameters have a direct correlation to the accuracy of the measurement. The installation of a pressure snubber or dampener could alleviate the need for the safety factor, as we'll discuss later.
Select a transmitter with the operating pressures at 50-75% of the calibrated range. This assumes that there are not many expected upsets that could cause large swings in pressure. If there are large swings (widening the range) due to process conditions, installing a second transmitter to handle the additional range should be considered.
Consider both the process temperature range and the ambient temperature range. The process temperature range represents the normal and abnormal temperatures the transducer will be exposed to via the process. The ambient temperature range gives the amount of temperature error to allow for without degrading performance outside the limits set by the application.
Install Properly
Accurate, reliable pressure measurements depend on correct installation. Start with location: A transmitter with a small display 50 ft. in the air next to a ladder becomes an operability issue. If maintenance personnel can't reach the transmitter, there is a maintainability, and possibly a safety, issue.
The manufacturer's installation literature describes how much vertical and horizontal distance is required around the transmitter to ensure it can be placed in and out of service easily.
Determine if and how the instrument will be taken out of service for maintenance and calibration without shutting down the process or injuring personnel with leaks or spills. A root valve and secondary block valve can isolate the instrument from the process. Some manufacturers will furnish this item as part of the transmitter assembly, or a manifold can be furnished as a separate item.
To keep maintenance costs down, look for a transmitter with modular components. For example, modularity would allow one piece of electronic circuitry inside the transmitter to be replaced in lieu of replacing the entire transmitter.
Impulse lines connecting the process to the transmitter should be kept as short as possible. One manufacturer estimates that impulse lines represent more than half the problems associated with instrument performance.
Instruments used in a liquid or condensable vapor should be mounted below the process connection. Impulse lines should be sloped down toward the instrument to prevent trapped gases inside the instrument or impulse lines. Transmitters should be bought with ports to allow venting of gas or draining as appropriate. Vertical lines are also generally sloped slightly to minimize the chance of vapor lock.
Instruments used in gas pressure measurement should be mounted above the process connection. Impulse lines should be sloped away from the instrument to prevent trapping liquids inside the instrument.
Route signal wiring away from power conductors per the spacing requirements listed in IEEE 518, Guide for the Installation of Electrical Equipment to Minimize Electrical Noise Inputs to Controllers From External Sources. Ensure that the signal shield is grounded only at one end and that conduit systems have intentional low points equipped with breather/drain assemblies for removing moisture.
Consider using block and bleed valves. The block and bleed valve has two purposes: for removing the instrument from the line without leakage, and for zeroing and testing the instrument. A bypass valve must be added if the measurement is differential pressure.
Dampeners, Seals, and Purging
Be aware of what types of transients could occur in the line where the transmitter is mounted. This is particularly important if a pressure transmitter is installed near a pump discharge. Pulsation dampeners are generally used to damp out process fluid pulsations, more often for signal fluctuations but possibly for protection against mechanical vibrations that might damage the transmitter.
One dampening technique is installing a pigtail in the impulse piping between the instrument and the process root valve connection, and some transmitters are available with built-in dampening. Signal pulsations are generally filtered by a dampener rather than time-delayed, so the output is an average of the pulsations. This raises the question of whether the transmitter will provide a representative signal.
Chemical seals serve several purposes in a transmitter installation:
* Preventing contact of potential noxious or corrosive process fluid with the transmitter.
* In certain cases, serving as a winterizing function in lieu of the electrical or steam tracing devices.
* Allowing remote mounting of a transmitter for better maintenance access (using a diaphragm and capillary-type seal). This can also alleviate some of the burdens associated with area classification if the diaphragm and capillary seal allows the instrument to be mounted outside the hazardous area. It is considered good practice to allow no more than 25 ft. of capillary tubing from the diaphragm to the transmitter. A downside to a capillary can be additional loop deadtime.
* Preventing solids or slurries from plugging the measurement element.
* Providing a larger surface area or process connection, which can improve sensitivity and help minimize plugging.
It is critical that the liquid in the seal be capable of withstanding the temperature at the process connection and the ambient temperature without freezing or gelling. The fluid should also be compatible with the process fluid so there is no major contamination problem should the seal break. Work with the transmitter or seal manufacturer to select the correct fluid.
Pay attention to the construction of the seal, and in general, look for fully-welded seals. In sanitary services, consider an approved self-cleaning seal. If vacuum is present, use a seal designed and constructed for that kind of service.
Purging is used to keep the instrument clear of process fluid that can cause plugging of the impulse lines or the transmitter. Purging is commonly used in applications involving solids, process fluids that are subject to solidification or plugging, and acid or basic fluids. The purge fluid must be compatible with the process and delivered at a higher pressure than the process, with check valves for backflow prevention. Reference 7 includes information on determining purge flow rates.
Before selecting the sensor type, if the specifier understands the measured process fluid and its characteristics in various temperatures and pressures, knows the conditions the transmitter will experience, and provides adequate room to install and maintain the transmitter, there's an excellent chance the proper pressure measurement technology will be applied.
Steven J. Marrano, PE, CEM, is principal engineer with Hazen and Sawyer, P.C., Philadelphia, an environmental engineering firm. Marrano is author of the Electrical Design and Specification Handbook for Industrial Facilities.
ALSO READ: Process variables and the art of calibrating instruments
References:
1. "A Resource for Pressure Control," Brayton Paul, Chemical Processing, August 1999.
2. "Smart Pressure Transmitters in the Field Bus Era," Steve Zager, Instruments and Control Systems, September 1996.
3. "Pressure Transducers: What They Are and How to Select One," Raymond Williams, Measurements and Control, April 1997.
4. Instrument Engineer's Handbook, Bala Liptok, (general definitions and pressure measurement sections).
5. Industrial Pressure, Level, and Density Measurement, Donald Gillum, ISA, 1995.
6. Process Measurement Instrumentation, American Petroleum Institute Recommended Practice 551, Washington, D.C.
7. Manual on Installation of Refinery Instruments and Control Systems, American Petroleum Institute Recommended Practice 550, Part I, Section 4: Pressure (out of print).
8. Manual on Installation of Refinery Instruments and Control Systems, American Petroleum Institute Recommended Practice 550, Part I, Section 8: Purges, Seals, and Winterizing (out of print).
9. "How Accurate Is Accurate?" Bill Mostia, CONTROL Magazine, June, July, and August, 1998.
Sponsored Recommendations
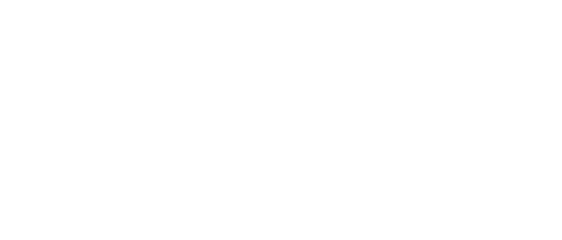
Leaders relevant to this article: