Production environments are getting smaller and more flexible. With fewer massive orders to fill, the industry is moving toward customized manufacturing. Addressing this demand means shifting to a low-volume, high-mix footing where frequent production line changeovers can be done efficiently. Increasingly, floor space needs to be adaptable, able to be quickly and easily reconfigured to build and assemble different products. Historically, for automated production lines this was a big challenge. Integrating robots into a production line required a significant amount of time and a high degree of technical expertise. Engineers would need to teach them new tasks, optimize processes, change out end-of-arm tooling and adapt software. The cost of these changes was substantial, often requiring the production line to be ramped down for weeks.
Significant innovation in cobot technology is enabling these transitions to happen much faster, sometimes in a matter of hours. Rapid advancements to sensor technology, machine vision and software allow operators to reposition and reteach robots at a much quicker rate. Vision systems not only allow for safe robot guidance, but dramatically improve productivity. These sensors can recognize the work piece and load the appropriate program needed for operation with less time required for teaching. Even the limited number of optimizations happen much more quickly. For example, if a grip position needs to be tweaked slightly, the operator can simply guide the arm to the appropriate position. Often, a few manual tweaks are all that’s needed to begin production on a new product line. Sometimes they’re not needed at all. For cobot manufacturers, these technological advancements are driving further changes to the production environment and shaping the cobot of the future.
Trend 1: Miniaturization and modularity
In a low-volume, high-mix environment, where production lines must be changed over rapidly and adding square footage is expensive, the emphasis is on repurposing and adapting existing floor space. For cobot manufacturers, this means the space for integrating their machines is getting narrower and narrower, and the design must adapt accordingly. But it’s not just space savings that’s needed. As the footprint of the cobot is required to shrink, the number of functions it must perform is increasing. In the consumer electronics space, we’ve been watching this same trend in desktop and laptop computers for years as companies continue to wring greater and greater performance out of increasingly smaller designs. This is precisely the trend that is now in full swing in automated production environments. Whereas a large-frame robot might be 1 ton or more, it’s not uncommon for cobots to be 20 kg or smaller.
This shrinking footprint creates a tremendous engineering strain. Cobots this small still require a lot of cabling and connectors for each axis and drive to ensure seamless power supply and data transmission. In addition, cobot joints, where movement is being actuated, must integrate multiple elements, often including a torque sensor, gear unit, motor drive and position sensor and power supply. Simply put, the connectivity, sensor and cabling design of the cobot can make or break performance. This is one of the most challenging factors facing cobot OEMs today.
The impact of miniaturization goes beyond robot design to include the control panel, as well. Beyond power, the added layers of data and communication mean the control panel is also responsible for managing an ever-increasing number of cobot functions. This puts a premium on small-form terminations in the panel. New customer segments are also changing control-panel design. As technology has improved, automation has become attainable for small to medium-sized production facilities, warehouses, laboratories and other applications. In these environments, control cabinets are being designed and built with specific architectures that match the precise requirements for a particular customer segment. Modular design is key for these highly specified, segment-driven control panels. It allows operations to scale quickly and grow the panels as needed, using standardized parts and even reusing parts when needed. It’s designed to reduce complexity, even in highly specific applications, by keeping the part numbers down and making it simpler to service and support while still meeting performance requirements.
Trend 2: One-cable and hybrid solutions
It’s no surprise that the move to smaller cobot designs is driving innovation in industrial communication. This is another key area of focus for robotic OEMs. As the robot arm becomes smaller, the industry needs fewer and smaller cables. This issue is compounded in cobot applications. In much larger standard robots, there is far more room in the arm and cabling is still often partially exposed. But in cobot applications, where the robot is working in tight quarters alongside humans, the cabling must often be completely internal despite the cobot’s smaller size. This means moving to hybrid—power and data—cables and smaller diameter cables like single-pair Ethernet (SPE). This is increasingly critical as the demand for higher-speed data continues to increase.
Originally introduced in the automotive industry, SPE technology is now seeing broader adoption in industrial applications, as well. It features Ethernet transmission over only one pair of copper wires in addition to power supply. For cobot manufacturers working with limited space, SPE technology allows them to reduce the number of wires from eight to two; improving arm flexibility and requiring fewer contacts on the interface. Not only is it simpler and a better use of space, but it also reduces cost due to the smaller number of wires required. For applications requiring higher currents and more power transmission, SPE hybrid connectors deliver data transmission up to 1 Gbps/600 MHz and power transmission up to 8 A. This far exceeds the previous power delivery of 1.36 A found in SPE connectors using power-over-data lines; and it comes in the form factor of an M8 connector. Without proprietary interfaces to deal with, SPE hybrid M8 connectors help system integrators bring a cobot up to production and streamline service/support.
SPE technology is smarter, too. Industrial networks are complex ecosystems that frequently require connections at the device level that are not only more costly, but also impair transparent communication. SPE technology enables the network to be IP-based, communicating transparently from the sensor to the cloud. This allows the end customer to replace traditional fieldbus and analog solutions at the field level, including gateways, and realize the advantages of IIoT. With SPE on the network edge, manufacturers can connect physical assets in their production environments, analyze the data from cobot sensors and make real-time decisions.
Trend 3: Torque, position and proximity sensors
Safety will always be a critical driver in cobot applications. Protecting the operation and the human teammate on the production line is of first importance. Often, a cobot is being introduced for safety reasons to begin with—to prevent repetitive strain injuries or protect the operator from harsh aspects of the application. But introducing humans and robots into the same application creates safety considerations of its own. Cobot applications primarily need to protect against human-robot collisions and, in the event of one, manage the force exerted on the human body. Here, force, torque, position and proximity sensors or laser scanners are key.
Preventing serious collisions starts with reducing their likelihood. Proximity sensors and laser scanners help the robot to detect the presence of a human or other object in its workspace and slow or stop movement. For applications where humans and robots need to work side by side, this allows the robot to continue work but at a slower speed to reduce the risk of injury to operators. Similarly, when the human leaves the workspace, the sensor detects this, as well, and speeds up work to ensure optimal performance. Torque sensors monitor the mechanical torque in robot joints to detect conditions where the torque level is high enough to harm a human nearby or damage the cobot itself. For many applications, torque thresholds can be established that will shut down work if exceeded. In the event of a collision, robots are programmed to stop movement immediately.
Improved safety isn’t the only advantage, though. The shift from power-limiting systems to power- and force-limiting systems with torque and position sensors has delivered improved accuracy, as well. Previously, a power-limiting system relied on measuring and controlling the position and the current being applied to an application and adjusting the robot accordingly. Torque sensors allow for a faster response time, which leads to safer and more reliable operation. By controlling the geometry of the steel and the sensing region, much more precise control can be achieved. Often, these torque sensors need to be designed specifically for a manufacturer’s robot to ensure optimal performance. In many cases they can also reduce cross-load errors—axial load, radial load and tilting moment—as well. But torque sensors increase accuracy in the end-of-arm tooling, as well. For example, in applications where constant pressure is applied, such as polishing a smartphone, it’s much more accurate to measure the force being applied rather than the current. This same advantage applies to assembly: for example, when the work piece and robot need to be very precisely aligned with the proper pressure applied to insert a small screw.
With the promise of automation bringing efficiency and greater understanding to all manufacturing operations, one thing remains certain: the industry will continue to need compact, safe cobots that perform with a high degree of accuracy. Tomorrow’s cobots will need to be smarter, too. The demand for more data to perform higher-order functions will depend, as it does in the production environment as a whole, on the cutting-edge connectivity and sensor solutions.
Daniel Pintar is senior manager, strategy and business development, robotics and motion, at TE Connectivity. Contact him at [email protected].
Sponsored Recommendations
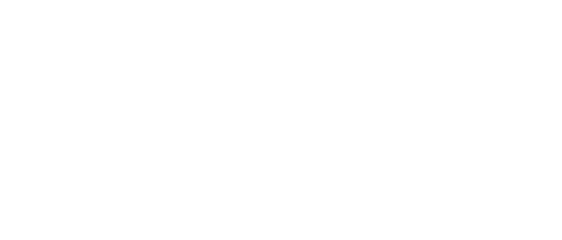
Leaders relevant to this article: