Multi-axis nanopositioning systems are widely used in most of modern nanotechnology and nanomanufacturing applications, such as scanning probe microscopy, nanofabrication and nano-patterning (e-beam lithography, for example), as well as various other scanned probe/tool-based metrology and process equipment. In these applications, the nanopositioning systems provide the displacement between the sample and the nanoscale manipulator, define the geometry of manufactured features with nanometer accuracy and implement high-precision alignment between different features.
Precision and accuracy are critical requirements for the nanopositioning systems used in nanotechnology and nanomanufacturing. The nanopositioning stages are able to provide nanometer scale displacement with a total motion range around at least tens of microns. To achieve such high performance, the design of the positioning mechanisms, the selection of the sensors and actuators and the implementation of advanced controllers need to be systematically investigated and integrated, which make the nanopositioning systems very different from conventional scale motor-based motion systems.
Most nanopositioning systems adopt some flexure based mechanisms. When the actuation force acts on the mechanism, the flexure joints or flexure structures are deformed to produce the desired displacement. Compared with conventional scale motion slides, flexure mechanisms provide infinite motion resolution and preclude friction and backlash found in sliding systems, thus the positioning resolution is not limited by friction or stiction. The trade-off for the resolution capability of the flexure mechanisms is their small range of displacement, since the flexure joints have to be operated at the elastic region of the flexure material. If a large motion range is a critical requirement, some low friction slides, such as air-bearing slides have to be selected to reduce the error from friction.
Many commercially available nanopositioner designs focused on single-degree-of-freedom axis modules, and multi-axis systems are realized by stacking individual units together. From a kinematics point of view, these designs belong to the class of serial kinematics systems in which the axes of motion are connected serially from a fixed base to the end effector to form an open kinematic chain. These designs are easy to implement and build from, and they have been used in many applications. The main problem in these designs stems from the relatively large inertias and relatively low dynamic stiffness of the resulting systems, which implies relatively low positioning bandwidths. In addition, these designs use different masses for motion in each axis that result in different natural frequencies and thereby performance capabilities for different axes, which in some instances are undesirable. Parallel kinematics designs overcome the above problems by having multiple kinematic chains that connect the base and end effector in a parallel scheme. Compared with serial kinematics designs, parallel kinematics designs usually have high structural stiffness due to their truss-like structure and shorter kinematic chains. Control design for serial kinematics systems is relatively simple because each actuation maps to a single direction of motion, orthogonal to the others and are thus decoupled. For the parallel kinematics systems, control design can be pretty complex; such decoupling is often not possible as the influence vectors of the actuators may not be orthogonal.
Also Read: Innovations That Could Change the Way We Manufacture
Actuators affect virtually every performance attribute (positioning resolution, repeatability, work space, bandwidth and size) of a nanopositioning system. Conventional actuators, such as motors, require transmissions and bearings, and are generally difficult to miniaturize. Voice coil actuators can ideally provide infinitely high positioning resolution. However, the coils for establishing magnetic fields cause heating, leading to large thermal deformations. Piezoelectric actuators are widely used in nanopositioning systems due to their faster responses, higher stiffness and larger force output. Piezoelectric actuators are easy to control and need very low electric current in static or quasi-static operation, which helps to alleviate heating problems. Furthermore, piezoelectric actuators have very good energy conversion efficiency since electrical energy is directly transformed into mechanical energy. One of the primary concerns when using piezoelectric actuators is their very small displacement output. For typical piezoelectric ceramics, the maximum strain capability is about 0.1%. To increase the displacement out, compound piezoelectric stack actuators need to be made by stacking multiple actuators together, and the lever transmission mechanisms need to be used. Other concerns regarding piezoelectric actuators include high driving voltage, unidirectional load capabilities (large compressive loads but a very low tensile load), aging and vulnerability to high temperatures.
Displacement sensors are essential to build a closed-loop nanopositioning system with improved accuracy. Their resolution and bandwidth have important effects on the performance of the closed-loop system. Widely used high resolution sensors in nanopositioning include capacitive sensors, linear variable differential transformers (LVDTs) and stain gauge sensors. All of these sensors can potentially provide nanometer scale resolution for nanopositioning systems with limited measurement range. Laser interferometers can potentially achieve sub-nanometer resolution and accuracy with measurement range in meter level. However, the equipment and its calibration are very expensive and complicated, and a well-controlled environment is generally required. The disturbances due to atmospheric temperature and humidity variations, air turbulence and vibrations can degrade the measurement accuracy.
Closed-loop controllers are indispensable for a nanopositioning system to achieve nanometer precision. Nonlinearities from the piezoelectric actuators, such as hysteresis and creep, as well as model uncertainties arising from flexure-based mechanisms, need to be compensated by the closed-loop control system to provide high positioning performance. Due to the frictionless motion from flexure structure, the flexure joints act as pure springs, and the nanopositioning systems generally have extremely small damping effect, which make the control design challenging for achieving a stable and high bandwidth system. Proportional-integral-derivative (PID) controllers don’t work well for such low damping nanopositioning systems, as it is difficult to provide enough stability margins to suppress the vibration. Proportional double integral (PII) controllers are the most common forms of controllers used for nanopositioning, since they can track ramp signals with zero steady-state error and are easy to implement. However, the best achievable bandwidth using PII controllers is very limited, due to the simplicity of such controllers. Many advanced controllers, such as the robust controller and iterative learning controller, have been developed recently to obtain high-bandwidth, high-resolution nanopositioning. These controllers can significantly improve the positioning performance but require much more computational power from the control hardware.
The fast evolution of nanotechnology and nanomanufacturing impose demanding performance requirements for nanopositioning systems. More innovations in mechanism design, sensing and actuating techniques are being introduced, and advanced control systems will continue to be developed to match the needs and offer new capabilities for emerging high-resolution semiconductor manufacturing and nanomanufacturing.
Continue Reading
Sponsored Recommendations
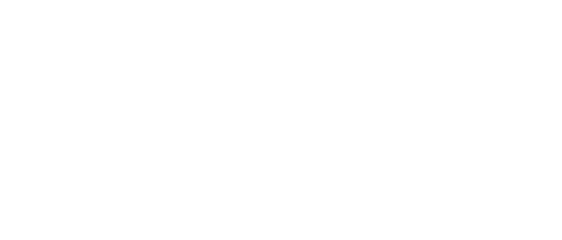
Leaders relevant to this article: