Ferenc Muranyi is strategic product group (SPG) leader for load cells/weigh modules at Mettler Toledo (MT). He holds a Ph.D. in physics from Budapest University of Technology and Economics and an MBA from SMC University.
Q: Precision measurement is a critical machine function in many applications. From design and installation to commissioning and operation, weighing accuracy and precision need to be ensured. What can machine builders do to reduce risk, expedite integration and facilitate operation and maintenance of load cells and weighing modules in equipment?
A: The straightforward thing to do is to select sensors that ensure both the specified accuracy and the entire system deliver the expected performance. Furthermore, today machine builders are moving to smart sensors connected to one common network throughout their machines. Standardized interfaces and data structures reduce the development time of the new generation of machines. Developers do not need to start from scratch; instead they can rely on previously programmed systems and can benefit from online available sample code. Standard communication interfaces also enable multiple engineers to work in parallel. Smart sensors greatly enrich the condition-monitoring and diagnostic capabilities of the machines because each sensor transfers status information together with the measured value. That helps the machine builder during installation and site acceptance and supports the operator during production. Various machine parameters can be optimized using the data from smart sensors to further improve production. In case of a sensor failure, the operator is notified without delay, and the sensor is replaced in minutes, thus resulting in short downtime.
Q: Intelligent devices provide data, which leads to operational visibility and better decision-making. How is Mettler-Toledo helping machine builders, system integrators and factories to enable digital transformation with products that lend themselves to data acquisition, analysis and contextualization?
A: Last year we launched a smart weighing transmitter, the IND360. This small device can connect almost any scale or balance to automation systems via a manifold of standard automation networks. With a recent device update, we enable direct cloud connectivity of the scale via on OPC UA protocol following the weighing companion specification. In the OPC UA message the IND360 also provides condition-monitoring data to help machine builders enrich the next generations of machines. We implemented SMART5 prioritized alarms based on NAMUR NE107. This provides a notification to the automation system, server or the operator, in case of any disturbance, where action should be taken to avoid out-of-spec products. Following this philosophy, we are launching a unique new smart single-point load cell family, called the SLP33xD-IOL. Please forgive me for the cryptic name and let me explain what we offer. This is an aluminum single-point load cell, with integrated connectivity and condition monitoring. These single-point load cells can be used as stand-alone sensors in any machine design to provide weight information. This load cell provides IO-Link allowing machine builders to connect the new smart load cell to any automation system, may that be Rockwell, Siemens, Beckhoff, Mitsubishi or any other. We also implemented the same SMART5 alarm system to notify the control system and operator when there is any trouble with the weight measurement. On board, advanced digital signal processing algorithms deliver higher accuracy weighing results. Compared to existing sensors we substantially improve linearity, hysteresis and precision. For example, we automatically adjust the load cell sensitivity when the temperature changes, thus increasing measurement accuracy.
Q: Can you explain the different classes of load cells—A, B, C and D? What does each one mean, and are there applications that require different classes of load cells?
A: These accuracy classes are defined by OIML R60. OIML is an international standard-setting organization, which works together with the World Trade Organization. OIML is helping countries and economies to put in place effective legal metrology infrastructures, which are then mutually compatible and internationally recognized. R60 is the international standard to classify load cells, and it sets the testing procedures. This standard defines the four classes of load cells, A, B, C and D. Each class has a lower and upper limit for the verification interval, nmax. The nmax is the maximum allowed resolution of the load cell in a legal-for-trade application (Table 1).
Class A | Class B | Class C | Class D | |
Lower limit | 50,000 | 5,000 | 500 | 100 |
Upper limit | unlimited | 100,000 | 10,000 | 1,000 |
The new SLP33xD-IOL load cells are available in the medium C3 and C6 accuracy classes. C3 and C6 fall into the category C, and have 3,000 and 6,000 verification intervals, respectively. The verification intervals are defined for legal-for-trade applications. A good example for a legal-for-trade application is buying apples in the grocery store. The price—commercial transaction—is defined by the product weight. To measure the product weight, a scale is used, which must be approved by the responsible authorities. However, in many machines there is no commercial transaction linked to the weighing result. In that case, the electronic resolution of the load cell determines the accuracy, meaning what is the highest, noise-free resolution. With the SLP33xD-IOL load cell, we can reach as high as 300,000 divisions. With this high resolution we reduce rounding errors common when the cells are configured for commercial transactions. For the 10 kg rated capacity load cell, that means 0.033 g noise-free resolution.
Q: What other types of sensing devices are useful in industrial manufacturing applications?
A: That depends on the application. For example, in a meat processing factory, the temperature must be kept low to avoid deterioration of the processed meat. That requires temperature sensors. Working with powders usually requires good control of the humidity; nobody wants to see clots in milk powder. That calls for the use of humidity sensors. In a chemical factory processing natural gas, sensors detecting any gas leakage are essential. There is a broad variety of sensors needed in various manufacturing applications, but all have common requirements. Machine builders want to work with standard interfaces, and the sensors must be “smart,” providing not only the measurement data, but also delivering status information. That will help the operators to achieve productivity and process safety.
Q: What recent improvements to sensing technology have made devices more innovative or efficient?
A: The principle of sensors is still the same. It is a device transforming a physical phenomenon into an electrical signal. Most of the cases we see use semiconductors for this purpose. And we can manufacture semiconductors on a microscopic or, even smaller, on a nano-scale. We see that sensors are getting smaller every year, and the cost of a sensor is shrinking. That enables machine builders to use more sensors on the production equipment, thus generating more data. Analyzing the captured data helps them to further improve the machines. A great enabler for efficiency is the standardized sensor interface, IO-Link. The foundations of this standard were laid down several years ago, but now it’s arrived on the market. Sensor-manufacturing companies offer a broad variety of sensors with the same interface. Automation control system providers actively promote this standard sensor-communication interface. Machine builders then benefit from the standardized interface, so all sensors speak the same language. In the future, we will likely see that advanced algorithms further improve the sensors’ and machines’ efficiency. I can also imagine that wireless data transmission in the sensor technology will gain ground, as we can further reduce sizes and energy consumption needed for wireless communication.
For more information, visit www.mt.com/slp33xd.
Sponsored Recommendations
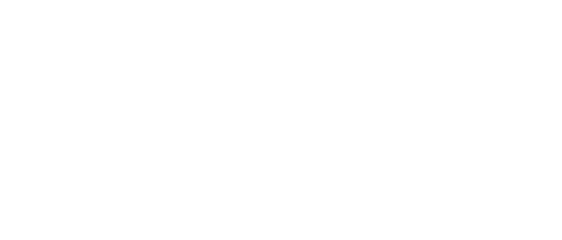
Leaders relevant to this article: