Reliable flow measurement is critical in processes that can’t be interrupted or where pressure loss is unacceptable. Ultrasonic clamp-on flowmeters can help. Depending on requirements, Proline Prosonic Flow W 400 or P 500 can be mounted noninvasively on the outside of the pipe, need only a minimum of inlet runs and are unaffected by aggressive liquids. Maintenance-free coupling pads ensure a stable measurement over the entire life cycle of the flowmeter.
High safety standards, transparent insights, flexibility, reliable measurements and long-term stable operation with zero maintenance have become important criteria for users.
Lauton Rushford is product marketing manager—flow at Endress+Hauser. He holds a bachelor’s degree in applied science, nuclear engineering, from Purdue University.
Q: Selecting the right flowmeter often depends on the flow rate range and desired level of accuracy. Any tips for obtaining accurate measurements across the entire operating spectrum and defining an acceptable margin of error for the control system?
A: Normally, this is driven by a specific application. In theory, every customer wants the most accurate process data, in the quickest time, and to utilize the information as a control point; however, in practice, this becomes much more difficult as costs associated to adding a “control point” within a process have increased due to many external factors. Our clamp-on portfolio—Prosonic P 500 and W 400—is aimed at applications where cutting piping is too costly, process compatibility can be an issue or need a movable process measuring point. By creating the ability to install the process on the pipe while utilizing the transit time technology we can ensure accurate measurement, up to +/- 1%, without any shutdown of process. Often, we are contacted about something called "usable turndown." Usable turndown refers to the full range of flow rates that a meter can handle while maintaining full accuracy. The larger this range is, the less customers need to worry about operating over a wide range of flow rates.
Q: Flowmeters can be designed for specific pipe diameters and materials to ensure proper installation and accurate readings. What sort of guidelines or recommendations can you provide for proper performance?
A: In the context of our Prosonic clamp-on portfolio, we aim to remove as many restrictive factors as possible for adding a measuring point to process piping and give more insight into what the process is telling us. With clamp-on technology by itself, we eliminate the need to cut pipe and greatly reduce the cost of installation for the measuring point. Temperature is also a restrictive factor associated to clamp-on technology due to the materials of construction and coupling pads/gel that allow the transducers to grip the pipe effectively. Endress+Hauser has tried to decrease that concern by introducing a high temperature sensor. This high temperature sensor uses a fully stainless-steel transducer and uses metallic coupling foils to ensure optimal connection to the pipe.
Q: What type of compatibility requirements are there for a flowmeter’s output signal—say, analog, digital, pulse—to the control system?
A: This is typically determined by the capabilities of the meter and the capabilities of the control systems. Customers have a variety of PLC/distributed control systems throughout the plant. Now Endress+Hauser Prosonic P 500 and W 400 have a few different options depending on the requirements of the customer. 4-20 mA outputs remain the most favorable outputs from the device to the PLC; however, pulse, frequency, switch and relay are also available with these devices. In terms of digital communications available on the Prosonic P 500 and W 400, these devices offer Modbus RS485 and HART.
Q: What types of installation constraints, such as space or accessibility for maintenance, should be considered when mounting a flowmeter?
A: Many clamp-on manufacturers require long straight pipe run requirements due to the nature of the technology and to establish a uniform flow profile. Endress+Hauser has developed a technology called FlowDC. FlowDC allows the use of two sensor sets to decrease that straight pipe run requirement down to two pipe diameters upstream and two pipe diameters downstream (Figure 1). This not only creates the opportunity for new measurement points to be installed in existing plants, but also decreases the piping costs on new plant builds.
Q: Flowmeters must be verified at regular intervals, as per quality regulations, such as ISO 9001. What sort of device-verification methods can be used that don't require interruption?
A: Heartbeat Technology is our built-in diagnostics/verification/monitoring tool that operates in the background of the measurement system. Heartbeat verification is a way for our device to perform a functional check of the device by using redundant references within the device as well as the “fingerprint” of the device back to how the device performed when calibrated at the factory. This allows for Heartbeat verification to be traceable back to its factory NIST calibration and comply with the ISO 9001 regulation. Similarly, Endress+Hauser has had this feature tested by TUV, a third-party internationally recognized laboratory, to prove that what we state is accurate. Verification and calibration are often used interchangeably in the industry. For Endress+Hauser, these two words mean different things. Calibrations are metrological performance assessments of the device in which calibration factors and zero-point values are examined under a fine-toothed comb to a total test coverage of ~99%. Verifications are internal/in-situ function checks of the device whereby using the fingerprint of the device and its redundant references we can give a very high total test coverage—greater than 94%—of the device without having to perform a true calibration.
Q: What type of functional-safety considerations should be made for flowmeter reliability, especially in hazardous areas?
A: Typically, the type of hazardous area determines the availability and reliability of the product. Applications in hazardous areas are defined by the likelihood of a dangerous atmosphere surrounding a meter. In the United States, there are two main classifications of hazardous areas—Class I, Div. 1, or Class I, Div. 2. The class refers to the type of hazard—gas for Class I, dust for Class II and vapors for Class III. Divisions are referring to the likelihood that those hazards are present. Division 1 is always present; Division 2 could be present if an upset condition were to happen. This often affects the types of instrumentation that can be utilized in these areas. There are requirements around the type of protection methods from an electrical aspect that also affect the way a meter must be wired up. Endress+Hauser has segmented their Prosonic P 500 and W 400 for two hazardous areas based around their main industries of focus. The Prosonic P 500 has the capabilities as well as an optional XP-rated housing for installation in Class I, Div. 1; whereas the W 400 is designed for installation in Class I, Div. 2. Another consideration for functional safety and installation in safety systems is the SIL rating of the software and hardware of the products. SIL refers to the safety integrity level (SIL) of a safety system. The higher the SIL rating, customers can reduce risk within their plant. Endress+Hauser has developed our devices with SIL 3 (software) and SIL 2 (hardware). These ratings are extremely important for maintaining safety and decreasing risk throughout the system.
For more information, visit www.us.endress.com.
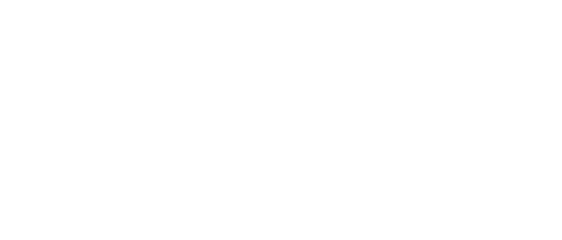
Leaders relevant to this article: