David L. Dechow, an engineer, programmer and technologist with expertise in the integration of machine vision, robotics and automation technologies, will present “The Fundamentals of Machine Vision” during A3's Automate Show in Chicago's McCormick Place on May 6 at 8 am. Dechow has served various companies and most notably was founder, owner and principal engineer for two automation system integration firms. Dechow is a recipient of the Association for Advancing Automation (A3) Automated Imaging Achievement Award and is a member of A3 Imaging Technology Strategy Board. As an educator within the machine-vision industry, Dechow has participated in the training of hundreds of engineers as an instructor with the A3 Certified Vision Professional program. Contact him at [email protected].
Machine-vision technology and its integration may not be well understood by many. Online, in-process, automated imaging is found in varying industries where machine-vision components perform tasks such as defect detection, measurement, assembly verification, robot guidance, optical character recognition and validation, flaw detection and code reading. Machine-vision components have evolved and are constantly improving. To make the best use of machine vision, a clear understanding of fundamentals can help to ensure specification and implementation for critical automation applications.
What is machine vision?
A machine vision system is a collection of components that acquire an image upon demand, and that can be configured or programmed to perform extensive analysis of the image to extract useful data about the object being inspected. These components include image sensors, cameras, smart cameras, optics and lenses, light sources, computers and software. The image itself may be full color or even might contain 3D or spectral data, but most applications are successfully executed with a standard 2D gray-scale image, which is processed more quickly and often at higher resolution with respect to cost.
Machine-vision systems interface easily with other automation components via discrete I/O signals, Ethernet and other common bus-level communication schemes. For certain applications, a machine-vision system can control the entire imaging and analysis process as a standalone operation without external communication. However, one unquestionable value of machine vision in an automation system is its ability to collect and archive discrete and statistical data about a process, providing the information that can help improve a production process.
In the analysis of each image, machine vision uses algorithms or tools on pixel-level data. Some of the common algorithms that may be incorporated in an application include edge extraction, contrast measurement, blob analysis and pattern matching, although machine-vision processors and/or software libraries offer dozens of analysis and processing tools including artificial-intelligence (AI) or deep-learning tools. These tools range from simple to complex and are usually combined to form a comprehensive inspection process suitable for the target application. It is important to have a good understanding of how each tool works with an image and produces data to select the proper set of algorithms to achieve the desired inspection results. However, there is a much more critical fundamental aspect to machine-vision system design and implementation that impacts every application from specification to integration: imaging.
Imaging as a foundation
Many of the components that support machine vision are related to the task of image acquisition, and for good reason. Proper imaging is the most critical aspect of any machine-vision application. The system’s ability to capture a correctly illuminated picture of the object to be inspected, with the object correctly presented to the system, can be an 80% or greater factor in the success and reliability of the inspection.
In terms of lighting components, the goal of machine-vision illumination design is to highlight objects or features of interest relative to the part’s background or other features. For some applications, this requires a significant level of knowledge, skill and creativity in designing the proper lighting scheme. Lighting and part position though are only the starting point.
All machine-vision imagers produce an image which is made up of small units called pixels. The number of available pixels for a given sensor is the system’s resolution, and resolution dictates how small an object, feature or defect the system can process given a specific overall field of view (FOV). The relative spatial size of a single pixel in each image is designated in millimeters per pixel or inches per pixel. Lenses play an important role, in that the lens determines exactly what FOV the selected sensor will produce and at what working distance.
Advanced users will also find an extensive variety of imaging sensors and camera systems that perform specialized tasks including 3D imaging, spectral imaging and detection of non-visible light in the ultra-violet and infrared ranges. Consider these components when standard imaging is not well indicated for a certain application.
Technology review
A core architecture still defines the makeup of almost any machine vision system. Lighting components are necessary to ensure the quality and repeatability of images. The remainder of the component technology generically comprises an imaging sensor, a computer and software. These components come in many forms with the most recognizable possibly being a smart camera or smart sensor.
These devices house a complete system in one package and include vision tools that are configurable, usually requiring no code. Closely related to these devices are hybrid systems that separate the computer from the image sensor, which in this case is enclosed and connected to the computer externally. This type of imaging device is generically called a camera or tethered camera. While this type of system can offer in some cases greater flexibility and scalability, configuration is still done through a user interface. At the other end of the architecture spectrum are imaging systems that are completely general purpose, using an industrial or embedded computer tethered with one or more cameras and often mostly custom programs using vision software libraries to perform more complex vision tasks.
With this kind of flexibility and number of options with many possible applications, one important aspect of the implementation of machine vision must be emphasized: integration.
Make it work
System integration for a machine-vision project is the process where significant value is added to components to create a complete inspection system or automation cell ready for use in an industrial environment. To be specific, one definition of integration is combining parts so they work together, forming a whole. Successful integration for an automation project involving machine vision requires not only significant technology‐specific skills, but also competency in a variety of engineering areas like mechanical engineering, controls engineering and computer science.
In all cases, there are key steps that should be followed to ensure a well-designed and implemented machine-vision system.
Best practices for machine-vision system integration include the following:
- Application needs and requirements: Analyze the needs of the existing operation, process or automation and gather all the details relevant to the targeted application without consideration of the machine vision technology. Consider what value will be provided. Describe the parts thoroughly and identify variations and special characteristics. Examine the entire production process and commercial considerations.
- Project specification or requirements specification: Identify function and operations—inspections, guidance measurements—that are to be executed by the system along with all the related performance metrics. Finally, detail the technologies that will enable the proposed system.
- Critical-path components: The machine-vision component rarely is just a placeholder in an automation system, but unfortunately it is sometimes treated as such. In virtually all systems, machine vision usually is the critical path component that, if it fails to perform as needed in the system, might thwart the overall operation of the entire project. Design the machine-vision technology first and then the remainder of the system around those critical components.
- Integration or project plan and organized task list: There are several good software tools available to help schedule tasks and manage projects. Use one to keep the project on track, but be sure to also address the details of the tasks.
- Installation—refine, not design, online: While there are occasions where some imaging, process or program development must be done after online installation, this should be the exception rather than the norm. The most efficient and successful projects are complete, tested and validated prior to final installation. If possible, design and install the imaging components—camera and lighting optics—within the production environment early in the process to gather representative production images for further off-line testing and programming before final installation.
- Validation plan: Always have and use a written validation plan for system acceptance testing. The document should outline the functional and operational criteria and metrics that indicate the system is working to specification. Even if the system has been validated prior to installation, repeat validation as the final step online.
Finally, machine vision has become a notably more sophisticated technology and engineering discipline. Overall, machine vision is easy to use and implement, and the value provided is significant. When the time involved in the integration process for machine vision is not a good economic investment for a company, seek out an experienced system integrator partner to reap the rewards achieved by using machine vision. With their broad understanding of and experience with machine vision products and applications, integrators typically can mitigate risk and guarantee a system that provides the best price/performance trade‐off.
Sponsored Recommendations
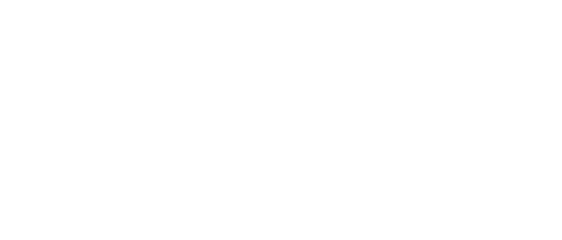
Leaders relevant to this article: