Moving PLCs, I/O and other control equipment closer to the input and output devices they manage has become standard practice among design professionals. It offers a number of advantages, one of which is that it allows for modular design of industrial manufacturing systems.
Modular system design means that individual subsystems can be completely fabricated, tested and function as standalone subsystems at the OEM before being delivered to an end user’s factory. This step greatly simplifies on-site installation and commissioning of a new manufacturing system and aids in future upgrades and expansion. It stands to reason that these same advantages can be realized if the necessary power devices, typically power supplies, are also moved closer to the devices they power.
The emerging distributed-power trend has multiple advantages. A unique approach to designing cost-effective systems using the standalone IP67 power supply has been increasingly adopted in the automotive manufacturing industry.
Early modular system design trends
[pullquote]In the early days of PLCs and other types of industrial control, it was common to put large controllers at a central location to control an entire manufacturing system. The industry evolved over the years with remote I/O, smaller controllers and various networking abilities that enabled large systems to be broken down into groups of smaller subsystems. This effectively allowed the control functions to be brought closer to the input and output devices. It is now becoming commonplace to even embed control functions in the input and output devices themselves.
One of the many advantages of this trend is that it allows larger industrial manufacturing systems to be broken down into groups of smaller subsystems, which are then interconnected together. Smaller subsystems typically make it much easier to design the control programs, especially when the subsystems can be well-isolated from the other subsystems in the overall system. In addition to software design advantages, there are hardware advantages. Because the control components and I/O cards are closer to the input and output devices, wire runs can be shorter, which not only saves the cost of wire, but also reduces related routing and installation requirements.
Installation and commissioning
One of the most important advantages of the distributed-control model is that on-site installation and commissioning is much more straightforward. With a typical centralized system, final system test at the OEM is often not practical, especially if the OEM is upgrading an existing system. As a result, all of the components must be first shipped from the OEM to the end user’s factory.
Next, extensive on-site hardware installation, wiring and software installation is required. Finally, the system is commissioned, which entails starting up the equipment, adjusting various parameters, testing for proper operation and troubleshooting any problems that come up. Unfortunately, a third party that is less familiar with the intricacies of the equipment than the OEM often performs these steps.
With a modular-system control design, installation and commissioning at the end-user location can be greatly simplified because the subsystem is isolated from the overall system. Much of the installation and commissioning work that was necessary in the centralized system can be done at the OEM location, even before shipping the equipment to the end-user facility. Obviously, this reduces the amount of work required at the end-user location.
In addition, it provides the OEM with more control over the reliability of the subsystem, thus improving the quality of the installed system and drastically reducing the amount of troubleshooting required. Ideally the subsystem is truly plug-and-play, so end users don’t need to be concerned with the ins and outs of getting the manufacturing subsystem to work.
Closer to devices
Of course, all this depends on how well-isolated the subsystem is from the rest of the system, since it still needs to be integrated into the overall arrangement. On the hardware side, one of the difficulties of isolating a subsystem is the power source.
It is very common for the majority of PLCs or controllers, I/O, peripherals and input and output devices to be powered by 24 Vdc, so it makes sense to distribute the power supplies closer to the input and output devices, as well. That way, many of the same advantages described earlier can be realized in the power wiring. Wire runs from the power supply to the devices they power are shorter and simpler. More importantly, the wiring can be wholly done at the OEM location, a step that reduces the on-site power concerns to merely connecting incoming power.
Some years ago, the automotive manufacturing industry recognized the potential for distributed power and started moving the power supply closer to input and output devices. Initially, automotive manufacturers deployed DIN-rail power supplies with lower wattages than required in a more centralized system.
IP67 power supplies
Figure 1: A standalone power supply with an IP67 rating not only saves the physical space that the power supply would have required, but it also eliminates the need to dissipate heat generated by a standard power supply.
There were still challenges to overcome. In a modular design, positioning components closer to the input and output devices usually meant that there was less physical space available for mounting those components. Also, traditional DIN-rail power supplies must be mounted in an enclosure, and the enclosure was often shared with other components.Since power supplies are heat-generating devices, oversize enclosures are usually required to dissipate the heat. This often resulted in an enclosure size that was too large to fit in the subsystem. Even worse, heat generated by the power supply increases the ambient temperature inside the enclosure, which can shorten the life of components in the enclosure.
The design solution that has proven successful within the automotive industry is to utilize power supplies that do not require mounting in an enclosure. Compact and rugged, a standalone power supply with an IP67 rating can be easily mounted directly on the equipment, right next to the components it is powering. Enclosures required for a PLC or any other components can be much smaller. This not only saves the physical space that the power supply would have required, but it also eliminates the need to dissipate heat generated by a standard power supply (Figure 1).
Standalone power
The installed cost of an IP67 standalone power supply compares very favorably with DIN-rail power supplies. The following simple cost analysis, comparing a traditional 100-W, 24-Vdc DIN-rail power supply configuration to that of an equivalent IP67 power supply, provides a comparison of the overall installed costs involved (Table 1).
The comparison chart demonstrates that the traditional enclosed DIN-rail power supply is much more labor-intensive, allowing substantial savings with the overall installed cost of the IP67 power supply. Labor costs are for assembly and installation only and do not include the expense of researching, specifying and ordering parts. This analysis also assumes that there would even be enough physical space on the subsystem to mount the larger enclosure required for the DIN-rail power supply.
Conclusion
Modular-design techniques offer a variety of economical, performance-driven benefits when designing industrial manufacturing systems. While this practice has been common with control equipment, modular distribution of power equipment provides substantial additional benefits in terms of reliability, ease of installation and commissioning and installed cost. By mounting the power supply on the subsystem close to the devices it is powering, higher reliability is possible because the majority of connections are made before the subsystem even leaves the OEM’s factory. This also simplifies commissioning, so the subsystem can be up and running with a minimum of on-site installation and troubleshooting time and cost.
Although distributing power can be accomplished with traditional DIN-rail power supplies, standalone power supplies are an ideal cost-effective alternative and can be installed in locations where available space is restricted.
ALSO READ: Power Supplies Get Smarter
Sponsored Recommendations
Latest from Power Supplies
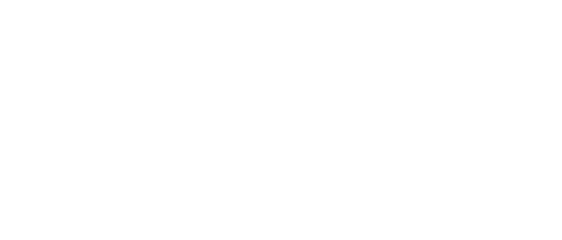
Leaders relevant to this article: